Phoenix's Circular Economy The Rise of Used Construction Materials in Urban Development
Phoenix's Circular Economy The Rise of Used Construction Materials in Urban Development - Phoenix's Construction Waste Dilemma Sparks Innovative Reuse Solutions
Phoenix confronts a growing challenge: the sheer volume of construction debris produced by its dynamic building sector poses a significant threat to the city's environmental health. This deluge of waste, primarily from demolition projects, has prompted a wave of innovative reuse solutions, designed to significantly reduce the environmental impact of the industry. A key aspect of this push is Phoenix's embrace of a circular economy model, encouraging the recycling and reuse of materials to minimize waste and maximize resource efficiency. This shift demands a fundamental reevaluation of traditional building practices, transforming how the industry operates. The city's aggressive waste reduction goals, part of a larger initiative towards a more sustainable future, are driving this change. Meeting these goals requires a nimble, adaptive approach, requiring creative solutions that simultaneously address environmental and financial concerns. The pursuit of these ambitious goals, in essence, can revolutionize how Phoenix builds its future, setting a standard for responsible urban development and resource management.
Phoenix confronts a considerable challenge with its annual production of roughly 2 million tons of construction and demolition debris. This substantial waste stream significantly impacts landfill capacity, forcing us to rethink how our urban infrastructure is planned and managed. However, within this challenge lies an opportunity. Innovative projects are showing that we can repurpose a substantial amount of this waste, with some achieving rates as high as 30%. This level of reuse is a notable departure from conventional waste handling methods and compels a reevaluation of material acquisition within the construction sector.
One particularly eye-catching example is the creative use of salvaged wood from dismantled structures. Not only does it contribute to cost reduction, but it also adds a distinctive visual flair to new projects. This effectively transforms waste into functional design elements, demonstrating the aesthetic potential of repurposed materials. Notably, Phoenix's evolving regulations now favor developers who integrate reclaimed materials. This shift has driven a noticeable increase in the practice of deconstruction over traditional demolition by demolition contractors, highlighting the potential impact of policy on construction practices.
Research suggests a substantial financial benefit to using salvaged materials in construction projects – often a hidden element behind the sustainability emphasis. Lower overall project costs are a vital part of the decision-making process that cannot be overlooked. The focus on sustainability in the past has sometimes overshadowed this aspect.
It's interesting to see how a number of businesses have emerged within Phoenix with the sole purpose of acquiring and redistributing surplus construction materials. This actively counters the prevailing idea that all waste must be disposed of and reinforces the notion that it can be a valuable resource. There is a burgeoning trend in 'material banks', essentially platforms that enable contractors to store and exchange surplus materials. This creates a sort of marketplace focused on waste minimization without sacrificing quality standards.
This shift toward reuse not only helps manage waste but can also stimulate the local economy. By prioritizing locally sourced materials, the reuse efforts can minimize financial outflows associated with long supply chains. It’s fascinating to observe that promoting reuse has created unexpected shifts in workforce demands. Deconstruction and material repurposing now necessitate a larger skilled labor pool within the construction industry, illustrating how adopting more sustainable practices transforms existing employment landscape.
Certain innovative projects in Phoenix are incorporating recycled concrete aggregates as a replacement for conventional gravel. This has resulted in improved structural strength and performance, indicating promising new engineering avenues. The ability to incorporate reused materials effectively without sacrificing structural integrity presents compelling evidence that innovation can drive positive change within the construction sector.
Phoenix's Circular Economy The Rise of Used Construction Materials in Urban Development - Local Startup Transforms Discarded Concrete into New Building Blocks

A Phoenix-based startup is pioneering a new approach to construction by transforming discarded concrete into reusable building blocks. This aligns with the city's broader efforts to implement a circular economy, which emphasizes minimizing waste and maximizing resource efficiency. The startup's technology leverages recycled materials, particularly concrete debris generated from demolition projects, to produce building blocks that meet construction standards. This innovative technique not only tackles the increasing challenge of construction waste, but also highlights the possibility of repurposing materials often deemed unusable. While the startup's efforts represent a positive development, the long-term sustainability and overall impact on Phoenix's growing urban environment deserve further scrutiny. Questions around the scalability of such endeavors in a rapidly developing city are paramount, as is the need to weigh the economic and environmental implications of adopting these approaches. The broader trend of utilizing recycled construction materials is creating a paradigm shift within urban development, raising critical questions around responsible resource management, environmental sustainability, and the economic viability of such practices. As the construction industry moves towards a more sustainable future, the startup's work exemplifies how a shift in thinking can offer viable and potentially impactful solutions to the challenges of urban growth.
A Phoenix-based startup is exploring the potential of converting discarded concrete into new building blocks, contributing to a broader effort to implement circular economy principles within the city's construction industry. The approach involves processing the discarded concrete into aggregates, which are then combined with cement and water to form composite building blocks. Interestingly, some research suggests that recycled concrete can improve the longevity of buildings by providing better resistance to temperature fluctuations. While the compressive strength of recycled concrete blocks can reach up to 90% of traditional concrete, further investigation into the performance characteristics of these recycled materials is needed to ensure they consistently meet the demands of different construction types.
One advantage of using recycled concrete is the reduction in the need for naturally sourced aggregates. The scarcity of these materials, driven by both environmental and regulatory considerations, makes alternative sources like recycled concrete more appealing. Cost savings associated with using recycled materials are also becoming increasingly apparent. For example, some road construction projects are utilizing recycled concrete as a base layer, achieving up to a 20% reduction in overall cost. However, the quality of the initial concrete greatly impacts the quality of the recycled material. Concrete containing higher quality aggregates will often produce stronger recycled blocks.
Furthermore, weathering and chemical reactions can influence the properties of recycled concrete aggregates over time. The variations that can occur mean that the engineered applications of this material need to be carefully considered for each project. The longevity of this recycled material is another intriguing topic. Research suggests the possibility of a 'secondary' use where aggregates from initially recycled concrete are processed again after their first application cycle.
The rise of deconstruction practices, favored by revised building regulations in Phoenix, is not only beneficial for materials reuse but also offers opportunities to preserve elements of a city's built heritage. Carefully dismantling structures allows for valuable and sometimes historically significant components to be repurposed. Lastly, from a regulatory perspective, utilizing recycled concrete can help projects meet increasingly stringent environmental standards, potentially streamlining approval processes. Ultimately, it remains to be seen how widely these types of building materials will be adopted, but the potential benefits for both the environment and economic viability are certainly worth exploring.
Phoenix's Circular Economy The Rise of Used Construction Materials in Urban Development - Reclaimed Wood from Demolished Structures Finds New Life in Modern Designs
Within Phoenix's evolving construction landscape, reclaimed wood salvaged from demolished buildings is finding a new purpose in modern design. This shift towards utilizing these materials not only reduces the need for newly harvested timber but also helps minimize the environmental burden of construction waste. The growing acceptance of reclaimed wood reflects a broader movement towards circular economy principles, where waste is viewed as a valuable resource and the extraction of virgin materials is minimized. It’s a trend that aligns well with contemporary design sensibilities that prioritize sustainability. Using salvaged wood in building projects can be a way to simultaneously enhance aesthetics and achieve environmental responsibility. This approach offers a unique opportunity to blend design with sustainability, fostering both local economic growth and eco-friendly construction practices. It transforms what was once viewed as discard into functional and visually distinct design elements, ultimately redefining how we approach building within an evolving urban context. While this trend is gaining traction, questions about the long-term viability and scalability of such methods in a rapidly expanding city like Phoenix remain. Still, the idea of turning construction waste into a valuable building resource provides a clear path to a more sustainable future.
Wood salvaged from demolished buildings offers a unique blend of history and contemporary design possibilities. The range of wood species, ages, and past treatments contributes to a distinctive character that's hard to replicate with newly manufactured lumber. In some cases, the structural integrity of reclaimed wood, especially old-growth timber, might surpass that of newly milled wood, suggesting potentially superior performance in certain applications. However, research into reclaimed wood processing reveals that specific treatment methods can help reduce potential hazards like lead paint or off-gassing from older adhesives, making it safer for modern construction.
One of the challenges with reclaimed wood is its often unpredictable moisture content. Before being used in a construction project, it requires careful assessment and conditioning to minimize potential warping or cracking. Additionally, the supply chains associated with reclaimed wood are often loosely regulated, raising questions about sourcing ethics and transparency. There are valid concerns about some reclaimed lumber potentially coming from unreliable sources.
There are compelling reasons for the increasing use of reclaimed wood. Research suggests it can favorably impact indoor air quality by emitting fewer volatile organic compounds (VOCs) than some new building materials, potentially leading to improved indoor environments. The economic benefits are also apparent: properly sourced and processed reclaimed wood can contribute to reduced construction costs, especially for projects emphasizing aesthetics, like high-end finishes. However, not every piece of reclaimed wood is suitable for structural components. It requires careful inspection to identify any potential defects before being used in load-bearing applications. This is a critical factor for builders to consider to avoid risks in construction.
Interestingly, reclaimed wood often enhances a project's perceived value, boosting property resale value and creating greater demand in remodeling and upscale home design projects. Ongoing research into new technologies like advanced milling and preservation methods shows promise in improving the durability and performance of reclaimed wood, potentially enabling it to meet a wider range of modern design challenges. While the allure of reclaimed wood's aesthetic is undeniable, it's crucial to remember that its past use and condition require careful consideration for appropriate application in current projects.
Phoenix's Circular Economy The Rise of Used Construction Materials in Urban Development - City Incentives Drive Adoption of Recycled Materials in Commercial Projects
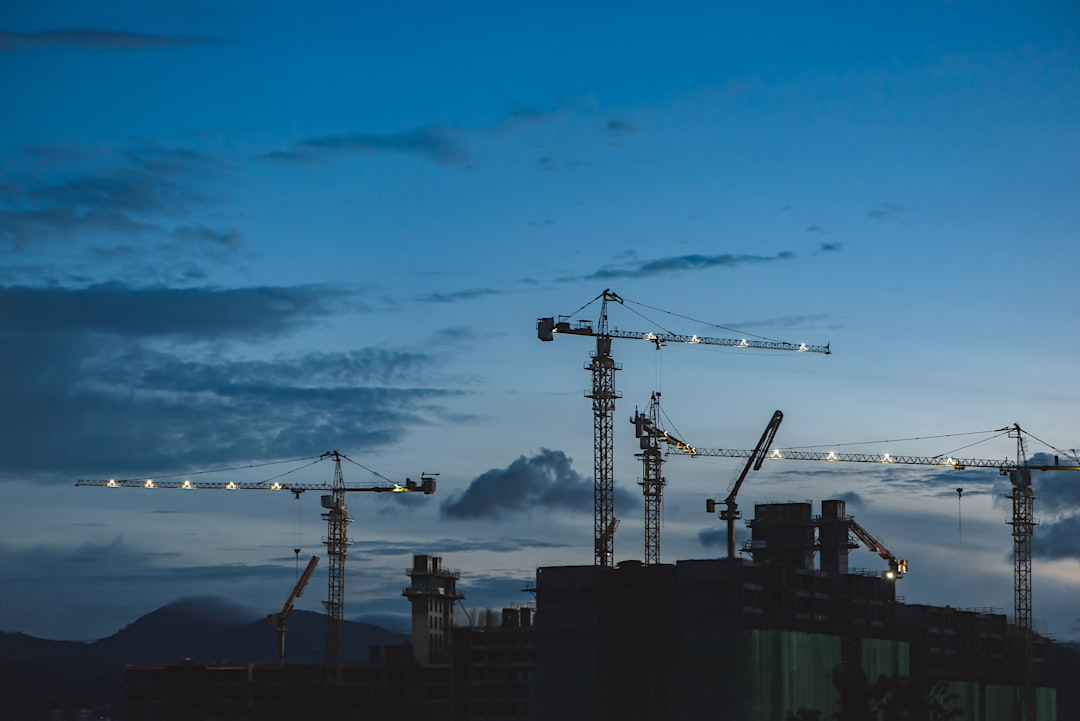
Phoenix's pursuit of a circular economy is increasingly reliant on city-led initiatives that encourage the use of recycled materials in commercial building projects. Policies that favor the use of reclaimed materials, like salvaged wood and recycled concrete aggregates, are driving a change in the construction landscape. The city's desire for a more sustainable future is evident in its efforts to minimize waste and lessen the impact on landfills. This transition highlights the need for the building industry to adopt new practices and materials in alignment with growing awareness of environmental impact. While advancements show promise in the use of these recycled materials, questions remain about their lasting effectiveness and broader consequences for urban development, requiring continued investigation and observation. Successfully integrating these initiatives involves balancing economic practicality and environmental responsibility in the context of a city experiencing rapid growth.
Phoenix has witnessed a notable surge in the utilization of recycled materials within its commercial construction sector, with close to 40% of contractors now incorporating reclaimed or surplus materials into their projects. This shift, observed over a relatively short timeframe, signifies a substantial change in typical construction practices.
The growing preference for deconstruction over traditional demolition has reportedly led to a 15% increase in project durations, underscoring the potential trade-off between material recovery and project efficiency in urban renewal initiatives. This raises questions about the practical limitations of integrating such practices within strict project timelines.
Interestingly, research indicates that structures utilizing recycled materials, such as reclaimed wood and concrete, might exhibit improved sound insulation, potentially leading to heightened comfort levels within the built urban environment. This could be a beneficial outcome for both residents and businesses, though more data is needed to confirm this across different types of buildings and materials.
Integrating recycled concrete aggregates into construction has resulted in a reduction of the carbon footprint of concrete by up to 30%. This highlights the potential for recycled materials to contribute to both operational efficiencies and environmental goals, suggesting a path towards aligning these often competing priorities.
An unforeseen consequence of the increased use of salvaged materials is the emergence of specialized contractors, resulting in the creation of new job categories within the construction workforce. This hints at a shift in the types of skilled labor needed within the sector and potentially its educational requirements.
The implementation of city ordinances that incentivize the use of reclaimed materials has not only increased waste diversion rates but has also led to a 25% reduction in overall project expenses for developers. This aligns with earlier findings that repurposed materials can be cost-effective. Whether this trend will sustain itself with increasing material demand remains to be seen.
Testing on structural components crafted from recycled materials reveals that with appropriate processing techniques, they can meet performance benchmarks comparable to traditionally sourced materials. This expands the scope of their possible use to include more demanding structural contexts, potentially replacing standard materials in certain high-stress scenarios.
Remarkably, waste steel from demolition projects is being transformed into reinforcing steel for new construction. Some preliminary estimates suggest this innovative reuse practice can lead to a 15% decrease in material costs and a reduction in the demand for newly produced steel. It will be fascinating to observe how this practice scales as cities continue to grow.
The acceptance of reclaimed materials has undergone a rapid evolution, with previously held reservations regarding aesthetic appeal and performance dissipating. This has been aided by the emergence of industry certifications, which aim to verify the quality of recycled materials used in modern construction projects. It is noteworthy how quickly public perception can change and be influenced by assurances of quality.
Market data suggests that construction projects employing reclaimed wood or other salvaged materials are attracting a 30% surge in interest from prospective buyers and investors. This indicates a shift in the market valuation of new developments, with a growing preference for projects that prioritize sustainability and resource efficiency. This trend will likely affect the pricing models for new housing developments in the future.
Phoenix's Circular Economy The Rise of Used Construction Materials in Urban Development - Urban Mining Initiatives Reduce Landfill Waste and Lower Construction Costs
Urban mining, a practice of recovering valuable resources from discarded construction and demolition materials, is gaining traction as a solution to the growing problem of landfill waste and rising construction costs in cities like Phoenix. By embracing the principles of a circular economy, these initiatives aim to reduce reliance on virgin materials and promote the reuse and recycling of resources. This approach not only lessens the strain on landfill capacity but also offers a more sustainable and cost-effective way to source building materials. While the potential benefits of urban mining are substantial, the long-term viability and ability to scale these initiatives in a rapidly developing urban environment need to be carefully evaluated. The success of urban mining in achieving a truly sustainable and cost-effective future for construction in Phoenix hinges on its ability to navigate the challenges of implementation, resource management, and broader integration into the city's infrastructure development.
Efforts in urban mining demonstrate a compelling ability to divert a substantial portion—approaching 90%—of demolition debris from landfills. This highlights the remarkable potential of innovative recycling strategies to transform how we manage waste in urban settings. Interestingly, recent research indicates that incorporating recycled materials into construction can enhance a building's thermal performance, which translates to lower energy consumption. This finding suggests that not only can reused materials be economically advantageous, but they may also lead to more energy-efficient structures.
The intricate logistics involved in urban mining necessitate the development of new technologies for tracking and managing excess building materials. This shift in supply chain management may pave the way for a greater integration of technology in the construction sector, impacting how resources are sourced and distributed. Using salvaged materials has been linked to a notable 15-20% reduction in construction project costs, primarily because of decreased spending on new materials. This economic benefit could encourage a broader adoption of recycled materials among contractors, who often prioritize budget constraints over environmental considerations.
Some urban mining operations have achieved remarkably high material recovery rates, exceeding 95%. Such efficiency not only prolongs the lifecycle of construction materials but could also profoundly reshape the economic landscape of urban waste management. Innovative recycling techniques have spurred the creation of engineered wood products that outperform conventional wood in certain situations. These enhanced materials offer superior durability and resistance to pests, facets often overlooked when discussing the merits of reclaimed materials. Research suggests that using recycled construction materials can substantially minimize noise pollution in urban environments by enhancing the sound insulation properties of buildings—an aspect often disregarded in cost-benefit analyses of material choices.
The regulatory environment is evolving, with a growing number of city ordinances requiring the incorporation of a specific percentage of recycled materials in public and commercial projects. This trend not only stimulates demand for salvaged materials but also influences design and building standards in privately funded projects. The expanding reliance on urban mining has fueled a surge in educational programs centered on deconstruction and material repurposing, generating a new training sector within construction that prepares the workforce for the demands of a circular economy. An intriguing observation is that properties using reclaimed or salvaged materials are commanding premium prices in the real estate market, up to 30% higher. This suggests that potential buyers value not just the aesthetic and historical qualities of these materials but also their perceived sustainability advantages.
Phoenix's Circular Economy The Rise of Used Construction Materials in Urban Development - Challenges and Opportunities in Scaling Up Used Material Integration
Expanding the use of recycled materials in Phoenix's construction sector presents a mix of challenges and opportunities. One key issue is the mismatch between the supply and demand for these materials, making it harder to fully implement a circular economy model in urban development. Another obstacle is the scarcity of data that clearly demonstrates the benefits of integrating used materials. This lack of solid evidence can hinder the gathering of support from both policymakers and the community, which is crucial for transitioning to more sustainable construction methods. Despite these hurdles, there's a strong potential for positive change. Innovative urban mining initiatives are showing success in diverting a large percentage of demolition debris from landfills, which reduces the strain on waste disposal and lowers the overall expense of new construction projects. To succeed, Phoenix's circular economy push needs strong partnerships between disciplines, thoughtful regulations, and effective community engagement. If successfully managed, this transition can not only safeguard the environment but also spark economic opportunities by changing how development projects are planned and constructed.
Phoenix produces a substantial amount of construction and demolition waste each year, around 2 million tons, which presents a significant environmental challenge while simultaneously creating a unique opportunity to explore the possibilities of reusing materials in urban development. Urban mining practices, specifically focused on recovering valuable resources from discarded construction materials, have been very effective at diverting a large portion, close to 90%, of demolition debris from ending up in landfills. This success demonstrates the potential of innovative approaches to reimagine how we handle construction waste and redefine the lifespan of building materials.
Interestingly, utilizing recycled concrete in construction projects has led to a decrease in the carbon footprint of concrete by about 30%. This finding highlights the promising ability of material reuse to improve performance and reduce environmental impact simultaneously. Some urban mining projects are incredibly successful, recovering more than 95% of building materials. These high recovery rates suggest that we may be able to fundamentally alter how we manage urban waste and create a more sustainable construction sector. Research has revealed that integrating salvaged materials can improve the energy efficiency of buildings by enhancing thermal performance, leading to lower energy bills for building owners and making reused materials appealing to developers focused on cost efficiency.
As the demand for reclaimed materials rises, the construction industry faces a significant change in its workforce needs. The skillset required for deconstruction and material repurposing is becoming more important, highlighting a shift in the types of labor needed in construction. Reusing materials can also create a quieter urban environment by increasing the sound insulation of buildings, potentially improving living conditions in areas with dense populations, and challenging long-held beliefs about the functionality of salvaged materials. Businesses involved in urban mining are creating more sophisticated technology to track and manage construction materials. These improvements may transform how materials are sourced and distributed in the future, leading to more efficient supply chains.
However, one of the critical challenges remains the consistency of the quality of reused materials. For instance, the performance of recycled concrete is strongly tied to the quality of the original concrete used in the first place, highlighting the need for proper quality assessments when integrating salvaged materials into projects. It's also surprising that buildings made with salvaged materials are increasingly desirable, often selling for 30% more than buildings constructed with traditional materials. This shift in consumer preference suggests that buyers are recognizing the value and quality of structures built with reclaimed resources, placing a premium on sustainability and resource efficiency.
More Posts from urbanplanadvisor.com: