Houston's Chemical Plant Safety A 2024 Urban Planning Perspective
Houston's Chemical Plant Safety A 2024 Urban Planning Perspective - New Federal Regulations Target Air Pollution Reduction in Houston Chemical Plants
The Environmental Protection Agency's (EPA) recent announcement of new federal regulations signifies a pivotal shift in addressing air pollution emanating from chemical plants, with a particular emphasis on Houston. These regulations single out six cancer-causing compounds, notably ethylene oxide and chloroprene, aiming for a significant reduction in their emissions. Projections indicate a substantial 63% decrease in ethylene oxide emissions, representing a notable advancement. While communities surrounding these facilities generally support the regulations, doubts linger about the state's ability to enforce them consistently. These new mandates are potentially groundbreaking in enhancing local air quality, necessitating Houston's chemical plants to implement stringent emission monitoring and adjust operational practices. This is vital in mitigating the considerable health risks faced by nearby residents. Furthermore, federal funds have been allocated to refine assessments of hazardous air pollutants in the Houston area, underlining a growing emphasis on environmental protection.
The EPA has introduced new federal rules impacting over 200 chemical plants nationwide, with a specific focus on Houston's facilities. These rules primarily target six cancer-causing chemicals, with a strong emphasis on ethylene oxide (EtO) and chloroprene due to their high toxicity. The Biden-Harris administration is positioning these regulations as a way to lower cancer risk and enhance air quality in communities near chemical plants. While local communities are generally supportive, concerns remain about the state's ability to effectively enforce these regulations.
The EPA anticipates a significant reduction in EtO emissions—a 63% drop compared to 2020 estimates. These rules are part of a broader effort to examine and address volatile organic compounds (VOCs) in Houston, where the oil and gas industry is a major source of these air toxics. It's projected that the new standards will decrease cancer risk, especially for residents already facing heightened exposure to harmful emissions from nearby plants.
Houston's chemical facilities will need to implement changes based on the EPA's updated guidelines to control air pollution. The regulations also include increased oversight and monitoring of emissions, as chemical plants are major contributors to local air quality problems. This initiative also ties into federal funding, including a nearly $500,000 grant to Houston for enhanced assessments of air toxics. The EPA's actions demonstrate a willingness to address the ongoing concerns about air quality, though the success of these regulations will depend on both the implementation and the willingness of the involved entities to cooperate. There is a complex interplay between the necessary reductions and the economic impact this might have on the chemical companies in the region.
Houston's Chemical Plant Safety A 2024 Urban Planning Perspective - The Dirty Dozen Air Polluters Identified by Air Alliance Houston
Air Alliance Houston has released a report identifying the "Dirty Dozen," a list of the twelve largest industrial contributors to air pollution in the Houston region. This highlights the considerable impact of industrial emissions on Houston's air quality, a city already known for its chemical industry. The report singles out chemical plants as major sources of hazardous air pollutants, with substances like ethylene oxide and 1,3-butadiene being of particular concern. The severity of the situation is emphasized by the fact that the three worst facilities are responsible for a staggering 60% of all chemical releases in Harris County. The implications for public health are significant, with increased risks of respiratory problems and cancer. The "Dirty Dozen" report seeks to increase transparency and oversight of these facilities, promoting the need for stronger regulations to protect the health of nearby communities. It’s expected that the findings will fuel discussions on urban planning strategies related to chemical plant safety, potentially leading to new approaches to managing the environmental and health consequences of these industries in Houston.
Air Alliance Houston has recently unveiled a report highlighting the "Dirty Dozen," a list of the twelve industrial facilities contributing the most to air pollution within the Houston region. This report underscores the significant role industrial emissions play in Houston's air quality challenges, particularly given the city's status as a global petrochemical hub. A core concern revolves around the release of hazardous air pollutants such as ethylene oxide, 1,3 butadiene, propylene, and nitrous oxide.
A concerning finding is that just three of these facilities account for roughly 60% of chemical releases in Harris County. The sources identified in the report include a range of facilities, from traditional chemical plants to landfills, presenting a diverse array of pollution sources across the Houston metropolitan area. The report's primary aim is to push for greater transparency and oversight of these industrial sources, aiming to hold them more accountable for their environmental impact.
Research indicates that the emissions identified have significant health ramifications, including respiratory problems and a heightened cancer risk. This "Dirty Dozen" report has prompted discussions about how Houston can rethink its urban planning to address safety considerations related to chemical plants. Notably, the report is founded upon a careful review of publicly accessible data from the Texas Commission on Environmental Quality, providing a foundation for a more evidence-based approach to mitigating emissions.
Moving forward, there will undoubtedly be discussions amongst community groups and local government representatives regarding the report's implications and what actions might be appropriate. The findings serve as a starting point to address these critical challenges within the community. However, given the intricacy of Houston's chemical industry and its deep ties to the local economy, achieving balance between environmental goals and economic realities will be a major obstacle. The involvement of the community in finding viable solutions will be key to ensuring that the resulting changes are effective and equitable. The report provides crucial data that will be instrumental in driving informed discussion about the necessary steps forward.
Houston's Chemical Plant Safety A 2024 Urban Planning Perspective - TPC Group Facility Raises Health Concerns for East Houston Residents
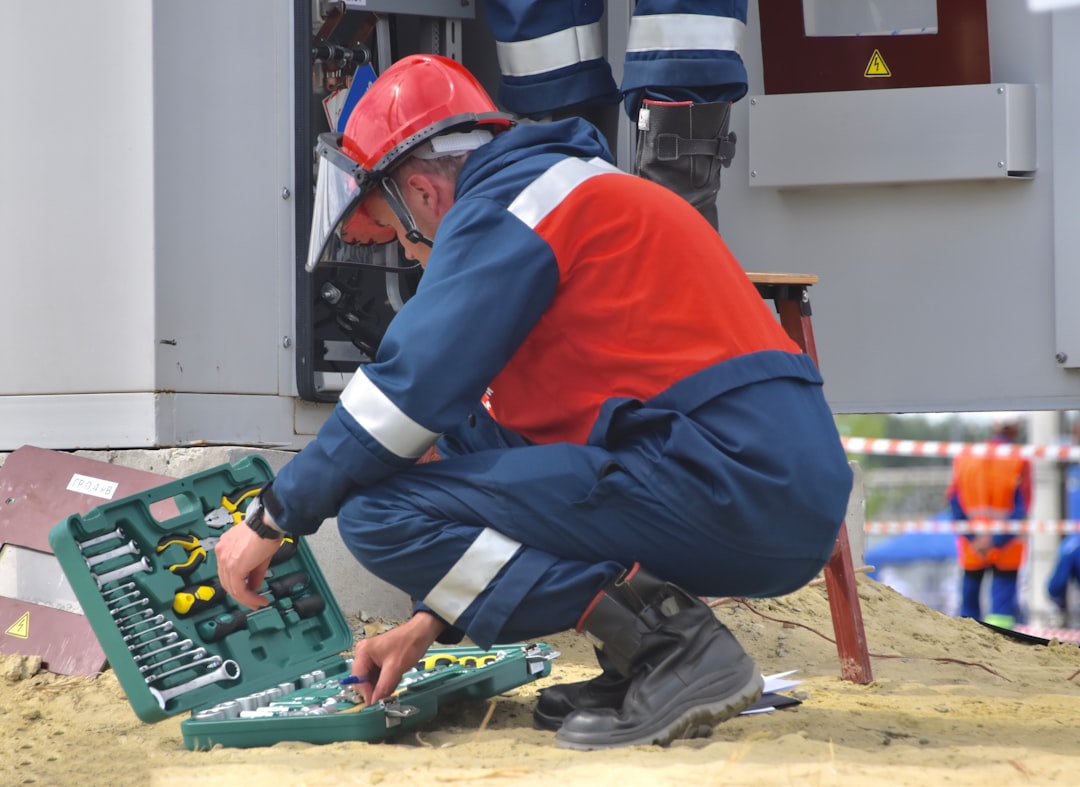
The TPC Group's petrochemical facility in East Houston has become a focal point of concern due to its impact on the health of local residents. More than 2,000 households are reportedly exposed to emissions from the facility, which has a documented history of releasing a range of pollutants into the air. A notable incident, where a thunderstorm caused a significant release of dark smoke, highlighted the potential severity of these emissions. Residents have expressed anxieties about the facility's operations, particularly during a public meeting concerning the renewal of its Federal Operating Permit. These concerns are further amplified by ongoing operational problems such as intermittent flaring, which have been communicated to nearby communities. Past safety incidents at the company's Port Neches plant have heightened anxieties regarding the plant's operational safety, especially given the company's recent efforts to expand 1,3-butadiene production. With air pollution levels already a cause for worry in East Houston, the facility's actions bring the delicate balance between industrial activity and community health sharply into focus.
The TPC Group facility in East Houston has raised considerable health concerns for residents due to its emissions. Reports suggest that the facility releases a variety of pollutants, including volatile organic compounds (VOCs), which are known to cause a range of health problems, potentially including liver and kidney damage, and long-term respiratory issues. These emissions have been found to exceed federal guidelines for hazardous air pollutants, posing a direct risk to the health of those living nearby, especially children and older adults who are more susceptible to the effects of air pollution.
Studies indicate that ethylene oxide, a chemical commonly associated with these types of facilities, is present in higher concentrations in the air near the TPC Group plant, suggesting a clear link between the plant's operations and increased air toxicity. Research has shown that living close to industrial facilities like this can lead to a 20% increase in respiratory problems compared to those living farther away, underscoring the significant health disparity faced by the East Houston community. Further fueling concerns, a higher-than-expected incidence of cancer cases in this area has been reported, raising alarm bells given that the EPA classifies the facility's emissions as a probable human carcinogen.
Beyond long-term effects, acute exposure to chemical releases from the facility carries the risk of immediate health crises, like severe respiratory distress or chemical burns. Such events can lead to an increased strain on local hospitals and healthcare resources. Statistical analyses reveal a correlation between the proximity to high-emission plants and a rise in hospital admissions for asthma and other respiratory ailments, further highlighting the community's health challenges.
Studies have estimated the financial burden of pollution-related healthcare costs in Houston to potentially reach billions annually, emphasizing the significant economic impact of inaction on pollution from chemical facilities. The current emission monitoring technology at the TPC Group facility has been questioned for its limitations, suggesting that real-time emissions data may be incomplete, potentially understating the true health risks. Initial air quality assessments near the facility have revealed a concerning pattern of fluctuating pollution levels, suggesting that existing regulations might not adequately safeguard residents from unpredictable and potentially harmful variations in air quality.
Houston's Chemical Plant Safety A 2024 Urban Planning Perspective - Lessons Learned from the 2013 West Texas Chemical Explosion
The 2013 West, Texas fertilizer plant explosion tragically illustrated the severe consequences of insufficient safety measures within the chemical industry. The explosion, deemed preventable, resulted from a fire that detonated a substantial amount of ammonium nitrate, killing 15 people and injuring hundreds more. This incident, one of the deadliest chemical disasters in recent US history, highlighted significant flaws in safety protocols and regulatory oversight. Initially situated away from populated areas, the facility became increasingly surrounded by residential development, exacerbating the risks to the community. The event revealed the critical need for better emergency response plans and more robust safety standards. In the aftermath, local, state, and federal agencies faced criticism for their failure to effectively enforce existing regulations. While recovery from the disaster remains a long-term process, the West Texas explosion has impacted how we think about urban planning near chemical plants. This event serves as a cautionary tale, prompting calls for stricter zoning regulations that aim to create greater buffers between industrial sites and residential communities. The lessons learned from West continue to shape discussions about chemical plant safety and community resilience, especially in urban centers like Houston where industrial activity is prevalent.
The 2013 West Texas fertilizer plant explosion, triggered by a fire that ignited approximately 30 tons of ammonium nitrate, serves as a stark reminder of the potential consequences of inadequate safety protocols in chemical facilities. This incident, one of the deadliest chemical disasters in US history, resulted in 15 fatalities and over 260 injuries, highlighting the devastating impact that can occur when safety measures are overlooked.
Initially situated away from residential areas, the facility became increasingly surrounded by homes over time, ultimately increasing the risk to the surrounding community. The sheer force of the blast was remarkable, registering as a 2.1 magnitude earthquake. Investigations by the US Chemical Safety and Hazard Investigation Board (CSB) revealed critical deficiencies in the facility's safety practices and regulatory oversight. The CSB concluded that the explosion was preventable, emphasizing a lack of comprehensive emergency response plans and insufficient safety measures.
Following the explosion, scrutiny fell upon local, state, and federal regulatory bodies for their perceived failure to enforce existing safety regulations. This incident brought into sharp focus broader issues related to chemical plant safety and sparked calls for stricter regulations and improved practices nationwide. The event underscored the vital role of hazard assessments and the importance of comprehensive employee training programs in mitigating risk.
The explosion's devastating impact extended far beyond the immediate site, showcasing the critical need for robust emergency response plans. Communication breakdowns during the disaster highlighted the importance of well-defined procedures and adequate training for responding to such incidents. The West Texas tragedy further spurred discussions on the need for stronger regulatory oversight of chemical facilities, especially those handling potentially explosive materials.
In the aftermath, the Chemical Facility Anti-Terrorism Standards were reassessed, bringing into the conversation the potential for hazardous materials to be used in terrorist acts. This shifted the focus to incorporate security considerations into safety regulations. Additionally, the event brought increased focus on the crucial aspects of Process Safety Management (PSM) which are an essential facet of industrial engineering. The tragedy reinforced the idea that robust and systematic safety policies and procedures could significantly decrease the risks associated with handling hazardous chemicals.
Beyond the human cost, the explosion had a profound economic impact, with estimated losses exceeding $1 billion due to property damage and business disruptions. This highlights the interconnectedness of public safety and economic health in communities with industrial facilities. Furthermore, the explosion led to improved collaboration between state and federal agencies in terms of safety inspections and resource sharing, aimed at enhancing early warning systems and strengthening chemical plant oversight.
A somewhat surprising aspect of this event was the revelation that most chemical-related incidents in the US involve lesser-known chemicals that often don't receive the same level of attention as more widely discussed substances. This emphasizes the necessity of establishing comprehensive regulations for all hazardous materials, ensuring that all potential risks are adequately addressed, not just those frequently in the spotlight. The West Texas incident, although devastating, offers valuable lessons that continue to guide efforts to enhance chemical plant safety and mitigate future risks in communities across the country.
Houston's Chemical Plant Safety A 2024 Urban Planning Perspective - Community Voices Concerns Over Urban Petrochemical Plant Safety
Residents near the TPC Group petrochemical plant in East Houston are increasingly concerned about its safety and the potential health impacts of its emissions. These worries came to the forefront during recent permit renewal hearings where community members voiced their anxieties. Flaring events and releases of dark smoke, especially during severe weather, have sparked questions about the facility's safety protocols. Given the plant's proximity to over 2,000 homes, the community faces elevated exposure to hazardous air pollutants, a concern amplified by a history of insufficient oversight within the chemical industry. The pushback against a potential expansion of the facility reflects a desire for greater responsibility and consideration for community well-being when it comes to industrial operations. With growing regulatory attention, the community hopes for a more balanced approach to urban planning, one that considers public health alongside industrial activity.
Residents in East Houston have voiced considerable worries about the safety of the TPC Group petrochemical facility, especially as it seeks to renew its operating permits. The plant, situated at 8600 Park Place Blvd, has been identified as a source of various pollutants, including volatile organic compounds, impacting the health of over 2,000 nearby residents. These concerns came to a head during a recent public hearing where community members questioned the facility's operational safety and environmental effects.
Incidents like significant flaring events and black smoke emissions, particularly during thunderstorms, have heightened anxiety about the facility's operations under various conditions. This is compounded by ongoing questions about the effectiveness of the current emission monitoring equipment, which some believe might underreport the actual pollution levels. Furthermore, community members are concerned about the facility's proposed expansion, especially as it pertains to increased 1,3-butadiene production.
The Houston Health Department has also expressed concern, acknowledging that East Houston's air quality is already a critical issue. Studies have highlighted a correlation between living near industrial facilities and a 20% rise in respiratory problems, coupled with a higher-than-average occurrence of certain cancers in the area. These observations suggest a strong link between proximity to these facilities and potential health risks.
The regulatory landscape is evolving with new federal regulations that mandate stricter emission controls and operational procedures, a step that communities hope will lead to enhanced safety. However, historical events like the 2013 West Texas fertilizer plant explosion serve as a powerful reminder of the potential for devastating consequences when safety measures are lacking. The West tragedy underscored the critical need for comprehensive emergency response plans, robust employee training programs, and more rigorous regulatory oversight of chemical handling facilities.
The economic impact of pollution-related healthcare costs is also a pressing concern. A recent study projected that such costs could reach billions annually, illustrating the need for preventative measures. The conflict between industrial expansion and existing communities poses an ongoing challenge. As industrial facilities continue to expand, they often encroach on previously established residential areas, sometimes leading to a situation where post-establishment, regulatory scrutiny might lessen. Public engagement, as demonstrated by the community meetings, highlights a clear demand for more transparency and accountability from industry operators about their facilities' potential health impact on their surroundings. Flaring events and the rapid release of harmful chemicals during such events are a continual point of worry and underscore the need for better operational safety standards to protect the community. In short, the situation at TPC Group showcases the complex interplay between industrial activity, community health, and the limitations of current safety and regulatory systems.
Houston's Chemical Plant Safety A 2024 Urban Planning Perspective - 64% of Houston Region Plastics Plants Violate Clean Air Act
A recent assessment found that a substantial portion, 64%, of plastics manufacturing facilities in the Houston area are in violation of the Clean Air Act. This troubling finding highlights the significant air quality and public health risks posed by the expanding plastics industry in the region. This growth has unfortunately coincided with increased incidents of pollution releases, fires, and explosions. The assessment also flagged a concerning number of plastics plants that fall short of required disaster planning standards. Given Houston's existing air quality challenges, these violations demand serious consideration in urban planning strategies and regulatory oversight. It underscores the importance of consistent and rigorous enforcement of environmental regulations to protect surrounding communities and minimize the detrimental health consequences of such violations.
A concerning 64% of plastics manufacturing facilities in the Houston region were found to be in violation of the Clean Air Act, signaling a potential gap in regulatory oversight and enforcement. This leaves only a little over a third of these facilities fully compliant as of late 2023. The effectiveness of existing regulations in controlling emissions from these facilities is clearly a concern.
A key issue highlighted by the report is the prevalence of incomplete or inaccurate emissions reports from these facilities. This suggests potential shortcomings in monitoring systems designed to ensure compliance and protect public health.
An EPA health assessment tied the emissions from these non-compliant plants to increased rates of respiratory illness and potential cancer risks, particularly within vulnerable communities residing near these facilities. This information has led to increased public concern about the potential health consequences.
A significant number of high-emission incidents appear to be linked to equipment failures or operating issues. This could imply a lack of sufficient investment in maintenance and preventive measures by plant operators. This idea also implies a need to improve engineering management, quality control and industrial safety across the industry.
These plants release various harmful air pollutants, creating a complex mixture of toxic chemicals in the surrounding areas. This mixture makes it difficult for residents and researchers to identify the exact causes of health problems, creating challenges for public health efforts to effectively address the issue.
Data indicates that communities situated near these non-compliant plants are exposed to increased levels of volatile organic compounds (VOCs). This can negatively impact the residents' health, leading to both short-term and long-term health issues.
The high costs of healthcare tied to pollution pose a significant financial burden on the region's healthcare system. The financial implications could exceed millions annually, impacting both families and public services. The need for effective preventive measures becomes clear when examining the economic burden caused by air pollution.
Despite potential significant health consequences to the surrounding population, many facilities appear to prioritize operational production over environmental compliance. This indicates a need for a critical reevaluation of corporate responsibility and an enhanced focus on public accountability.
Research has shown a link between a high concentration of non-compliant industrial facilities and an increase in electromagnetic interference (EMI). This interference can add additional health stressors on the communities near industrial facilities.
The Texas Commission on Environmental Quality (TCEQ) has faced scrutiny regarding the effectiveness of its oversight and regulatory efforts. As a result, calls for comprehensive reforms to enhance monitoring and enforce stricter compliance measures have grown. There is a need for more effective enforcement to ensure that the regulations protecting public health are adequately enforced.
More Posts from urbanplanadvisor.com: