The Engineering Marvel of Chicago's Willis Tower A Floor-by-Floor Analysis of its 110 Stories and Architectural Innovation
The Engineering Marvel of Chicago's Willis Tower A Floor-by-Floor Analysis of its 110 Stories and Architectural Innovation - Nine Individual Tubes Form the Foundation of Willis Tower Design 1974
At the heart of the Willis Tower's design, completed in 1974, lies a system of nine separate, interconnected tubes forming its structural core. This "bundled tube" concept was a novel approach, providing the tower with exceptional stability and enabling it to reach its impressive height. The unique arrangement of these tubes, each with 75-foot sides, creates a visually distinctive profile and plays a crucial role in its wind resistance, a necessity given Chicago's often blustery conditions. The tower's designers cleverly minimized steel usage—a testament to the system's efficiency—while still achieving extraordinary scale. This innovative design approach has had a lasting impact, shaping skyscraper design globally and solidifying the Willis Tower's place as a pioneering achievement in structural engineering.
The fundamental concept behind the Willis Tower's structural integrity, as realized in 1974, rests on a system of nine separate, interconnected tubes. These tubes, each with a unique height, work together in a bundled arrangement, forming the backbone of the building's stability. One could almost see a hint of inspiration from the arrangement of a cigarette pack in the staggered heights of the tubes, but whether intentional or not, this peculiar geometry contributes to the building's wind resistance and adds to its distinctive appearance. Notably, the way these tubes interact allows the Willis Tower to resist strong winds—a critical consideration for its height and location in Chicago, where wind can be a substantial force.
This design approach led to a considerable reduction in steel usage compared to earlier skyscrapers. Notably, it required only 33 pounds of steel per square foot, considerably less than the 66 pounds required for the Empire State Building, illustrating a move toward efficient structural design. Each tube itself measures a significant 75 feet on each side, which combined creates an immense 225-foot dimension on each side of the entire structure. This provides a sense of the sheer scale of these tubes, and their contribution to the enormous size of the Willis Tower. It's fascinating how the design of these tubes, in tandem with the staggered configuration, was a step towards minimizing material use and enhancing stability in such a tall structure. While effective, one can't help but ponder if there were other ways to reach such goals, or perhaps further reductions in materials could have been achieved through further refinement.
The Engineering Marvel of Chicago's Willis Tower A Floor-by-Floor Analysis of its 110 Stories and Architectural Innovation - Floor 66 The Mechanical Hub That Powers Chicago's Tallest Building
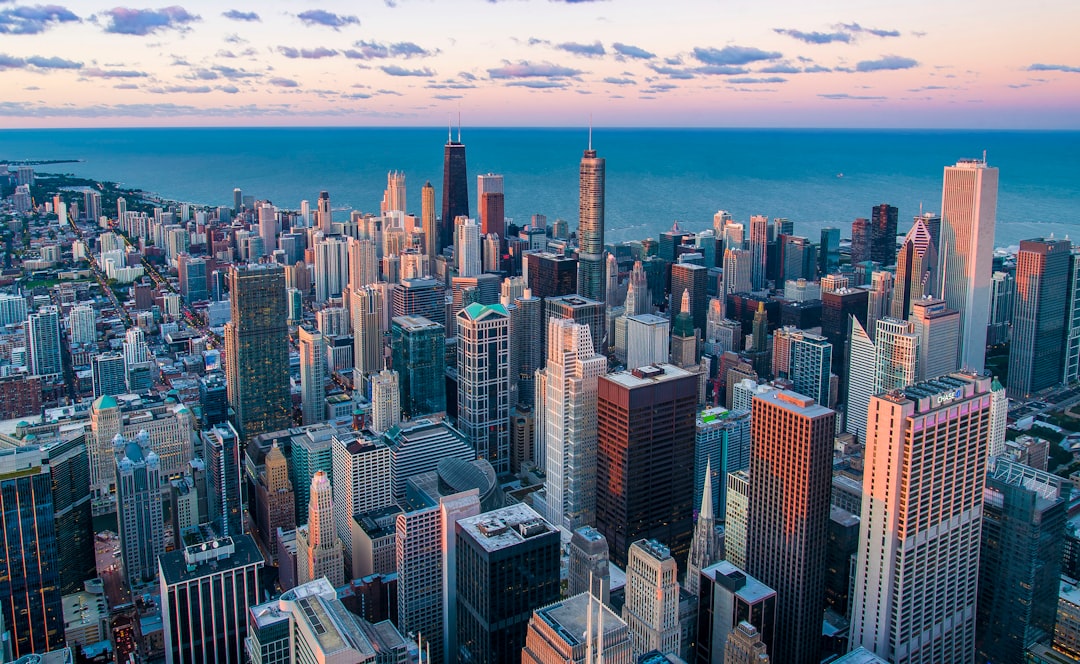
Floor 66 of the Willis Tower is the central hub for the building's mechanical systems, effectively the engine room that keeps Chicago's tallest building running. It's here that a vast array of essential equipment resides, ensuring everything from heating and cooling to power distribution functions flawlessly. This floor's design speaks volumes about the intricate planning that goes into maintaining a building of such scale, where efficient operation is critical. The engineers had to find a balance between the need for enough space to house all this equipment and the need to ensure easy access for maintenance and repair.
The existence of this floor emphasizes an often overlooked aspect of architectural ingenuity: the unsung heroes that keep the building running. Floor 66 is a prime example of how innovation isn't always about visible design elements, but also about the unseen systems that support the structure and the people who inhabit it. In a time when building efficiency is more important than ever, this mechanical heart of Willis Tower stands as a testament to the enduring legacy of skillful engineering. It highlights the continuous need for thoughtful design, not just for what's visible to the eye, but also for what's required to keep a towering structure like the Willis Tower alive and functioning. While we may be drawn to the architectural wonder and the breathtaking views, it's floors like 66 that remind us of the complexities that exist beyond the facade.
Floor 66, nestled within the towering structure of the Willis Tower, takes on a crucial role as the building's mechanical heart. It's here that the complex web of systems that keep this urban giant running smoothly comes together. From managing heating, ventilation, and air conditioning (HVAC) to providing crucial water resources and even handling backup power, Floor 66 is a testament to the intricate workings required to maintain a structure of this scale.
One quickly recognizes the sheer energy demands of maintaining such a massive building when looking at the HVAC systems on Floor 66. Annual energy consumption reportedly exceeds 5 million kilowatt-hours, a staggering amount that highlights the ongoing challenge of powering a building that reaches such heights. It raises the question, what innovative approaches can engineers develop to lessen the energy demands of such large buildings?
Chicago’s notorious winds also pose a challenge. Engineers have incorporated damping devices into the mechanical systems to help minimize the building's sway in high winds—winds that can easily reach 70 miles per hour at the tower’s upper levels. These mechanisms are a reminder of the continuous battle engineers wage to ensure stability in tall structures, particularly in locations prone to severe weather.
Further examining the mechanical functions on Floor 66, we find that it also contains large water tanks providing essential services to the upper floors. Maintaining sufficient water pressure at such heights requires a clever approach, ensuring adequate supplies for both drinking water and fire suppression systems.
Interestingly, the mechanical systems are not just about functionality, but also safety. Robust backup generators on Floor 66 are a critical component for maintaining operations during a power outage, highlighting the vital need for redundancy in critical systems. These features are paramount for the safety and well-being of both occupants and the building itself.
Adding another layer of complexity is the sheer number of elevators that serve the Willis Tower. Over 100 elevators travel up and down this vertical city. Maintaining these systems is no small task. Elevated maintenance access on Floor 66 is a fascinating aspect of the building's design, allowing for easier repair and upkeep of these vital components.
Looking further into the operations of Floor 66, we see the utilization of advanced Building Management Systems (BMS). These sophisticated systems allow for real-time monitoring and control of various utilities, promoting reliability and efficiency. Such systems are critical for detecting potential malfunctions swiftly and ensuring the entire mechanical network functions optimally.
An interesting aspect of Floor 66 is the integration of thermal mass techniques into the design. It captures and regulates the heat generated by the mechanical systems. This approach, in turn, helps minimize the energy needed to regulate temperature, improving both efficiency and comfort within the building.
It's important to remember that the Willis Tower stands in a location susceptible to seismic activity. The engineers included features within the mechanical design on Floor 66 to address this potential risk, further enhancing the tower's overall stability and resilience.
Finally, we find that Floor 66 also serves as a load-bearing level within the structural framework of the building. This reveals a deeper integration of mechanical systems within the tower’s core design, a brilliant example of multi-functionality in engineering. This thoughtful approach demonstrates how engineers can utilize various elements of a building's design in multiple ways, optimizing stability and functionality throughout the entire structure. Floor 66, in this regard, becomes a testament to the ingenuity of design and planning that makes a structure like the Willis Tower possible. While effective, it's also a compelling area to wonder if there are further refinements that could be implemented to enhance either energy consumption or perhaps further integrate the mechanical systems into the core design.
The Engineering Marvel of Chicago's Willis Tower A Floor-by-Floor Analysis of its 110 Stories and Architectural Innovation - Floor 103 Glass Balconies Engineering Breakthrough in Structural Load Distribution
The 103rd floor of Chicago's Willis Tower features "The Ledge," a series of glass balconies that showcase a significant advance in how buildings manage weight and stress. These balconies extend 43 feet out from the building, offering visitors a unique perspective 1,353 feet above the city. The design of each balcony is notable for its use of three layers of half-inch thick, low-iron laminated glass. This allows each balcony to support an impressive five tons of weight. This innovative glass structure is a great example of how engineers can create a thrilling visitor experience while ensuring structural soundness. The process to develop The Ledge was no small feat, taking over a year of engineering and an additional six months to construct. The Ledge, as a result, isn't just a visually stunning addition to the Willis Tower but a testament to how careful engineering can bring unique architectural features to life, further solidifying the Willis Tower's reputation as a symbol of architectural excellence and structural innovation. One might wonder, however, if the materials used were the most suitable or if other options might have provided even more durability and safety.
Floor 103's glass balconies represent a significant engineering feat in managing structural load distribution. The design goes beyond mere aesthetics, focusing on the inherent strength of structural glass to provide those breathtaking views while adhering to rigorous safety standards. The engineers tackled the challenge of evenly distributing both the weight of the structure itself (dead load) and the weight of visitors and any furniture (live load) across the balcony's cantilevered design. This distributes the stress across a larger area, minimizing the strain on the balcony's attachment points and the supporting beams.
A noteworthy aspect of the design is the edge treatment of the glass panels. A specialized interlayer is incorporated to significantly enhance the load-bearing capacity of the glass. This detail is crucial for withstanding the pressures and potential impacts the balconies might face at that height, especially considering the powerful winds Chicago is known for.
Moreover, the engineers factored in thermal expansion and contraction caused by temperature fluctuations. They carefully chose materials that accommodate these changes without compromising the structure's integrity. This is an example of how even seemingly minor elements, like temperature shifts, are accounted for in the overall design. It’s also interesting to see that they considered the potential for seismic activity. Flexible attachment methods allow the balconies to move slightly during an earthquake, helping to dissipate the energy of the seismic forces and maintain the structural integrity.
Furthering the design's elegance, utility lines for water, electricity, and other services are subtly hidden beneath the balconies, maintaining the visual appeal. This reveals the effort made to integrate practicality with design. This floor also showcases how the building combats Chicago's renowned wind. A system of wind bracing minimizes the sway, ensuring the balconies remain stable and secure, even during strong gusts. The commitment to safety is demonstrated through rigorous impact resistance testing, simulating heavy snow loads and ensuring the balconies can withstand such intense conditions.
Furthermore, the engineers had to go beyond standard residential glass balcony design, which typically only considers static loads (weight). They had to account for dynamic loads like wind uplift and vibrations from nearby traffic. By considering a wider range of forces, the engineering ensures the balconies' security in a variety of conditions.
Finally, the glass itself benefits from cutting-edge technology that enhances both its clarity and durability. Specialized framing and anti-reflective coatings reduce thermal breaks, contributing to energy efficiency while upholding the overall aesthetic design. The successful engineering of Floor 103's glass balconies exemplifies the complexity involved in designing for extreme conditions and reveals the importance of meticulous planning in load distribution within such a large and complex structure. One wonders if there are further avenues for innovative load-bearing systems in the future.
The Engineering Marvel of Chicago's Willis Tower A Floor-by-Floor Analysis of its 110 Stories and Architectural Innovation - Emergency Systems at Willis Tower Wind Monitoring and Fire Safety across 110 Stories
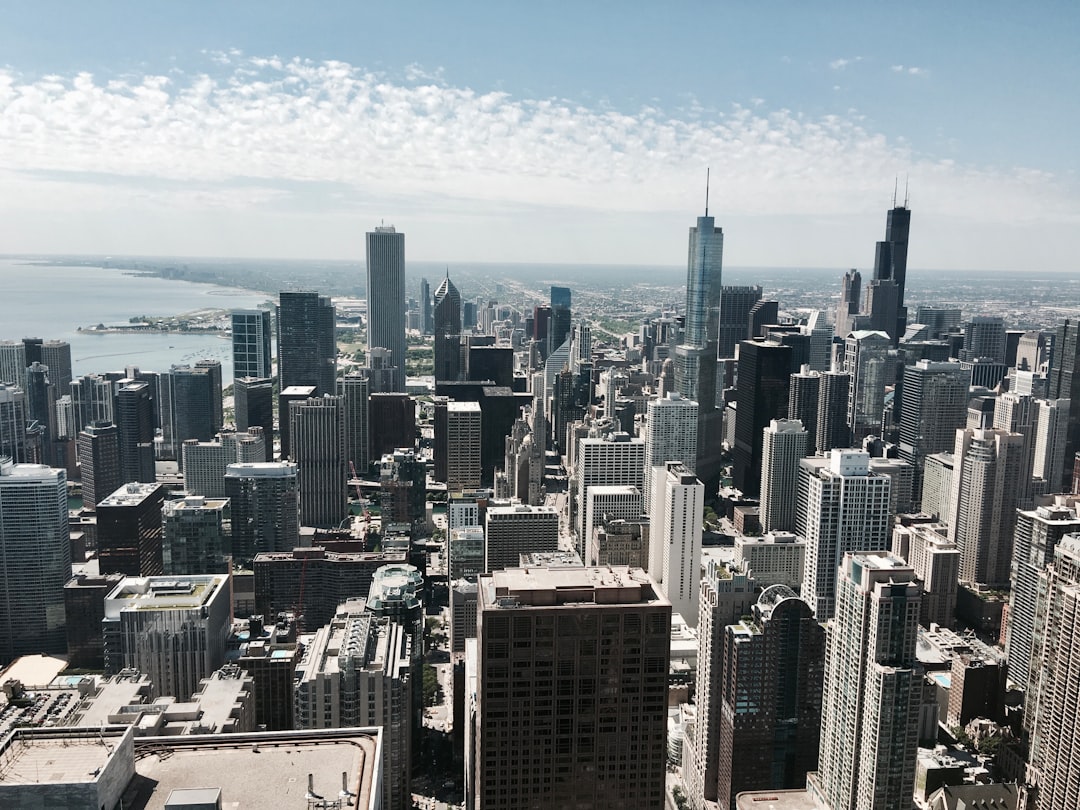
The Willis Tower's 110 stories demand an intricate network of emergency systems to ensure the safety of occupants and visitors. Wind monitoring plays a vital role, given Chicago's often severe weather. The building's design, which naturally allows for some sway, is continuously monitored to ensure it remains within acceptable parameters. While the building has a designed sway, it's still a testament to the ingenuity of engineering that such a tall structure can be built to withstand high winds. Fire safety is another critical component, with the building incorporating a range of systems to meet modern standards and regulations. These systems have been enhanced through major renovations, illustrating a continuous effort to prioritize safety. The building's structural design, developed decades ago, remains central to the success of these emergency systems. It highlights the important relationship between a building's structure and its ability to maintain safety. In the future, as we design taller buildings for increasingly dense urban environments, these concepts will become increasingly important for ensuring safety in similar structures.
Given the Willis Tower's immense height and location in a city prone to strong winds, it's no surprise that emergency systems are a critical part of its design. The building utilizes a sophisticated network of wind sensors to constantly monitor wind speed and direction. This information is then used to adjust the building's response, aiming to minimize sway and ensure safety during high-wind events. It's interesting how such a system allows for the tower to react in real-time to external forces, much like a sophisticated feedback mechanism. However, one might wonder if there are further ways to enhance this technology for even more responsive and adaptive behavior.
Throughout its 110 floors, a robust fire safety system has been installed. This includes a comprehensive network of alarms and detectors to quickly identify any potential fire hazards. Fire-resistant materials have been used throughout the structure, which is particularly crucial given the sheer vertical distance involved in an emergency. It's fascinating how the design addresses a multitude of potential fire-related scenarios, from the earliest detection to the use of materials that can better resist the spread of fire, but questions about the long-term efficacy of the materials used and their resistance to future threats remain.
The more than 100 elevators also integrate safety mechanisms that are notable for their redundancy. They rely on both mechanical brakes and electronic sensors to detect and react to unusual conditions, increasing passenger safety. It's ingenious how they've layered these safety measures, but one does wonder if a more advanced and AI-based system would provide more sophisticated monitoring, leading to a greater level of safety and preparedness.
While Chicago isn't known for its seismic activity, the tower's design takes this into consideration. Flexible connections are incorporated into the structure, allowing it to better tolerate minor seismic events. This reveals that even in locations where major earthquakes are rare, the engineering team has factored in potential seismic risks, an admirable precaution. It is interesting to wonder how these features would perform in a more significant seismic event.
The tower's design includes designated refuge areas on each floor, which serve as secure spaces in case of a fire or other emergency. These areas are well-marked and frequently used in drills, which highlights the tower's commitment to preparedness. The implementation of these spaces does show the emphasis on occupant safety in an emergency situation, but the effectiveness and overall utility of the spaces in the event of a genuine emergency still requires consideration.
Floor 66, the heart of the building's mechanical operations, houses a range of advanced thermal management features. This includes things like insulated pipes and heat recovery systems, contributing to a more efficient use of energy within the tower. It’s a brilliant demonstration of integrating energy efficiency into the operational aspects of the tower. However, the long-term impact of these technologies in the face of climate change and rising energy costs is yet to be fully determined.
The Willis Tower also boasts redundant power sources, including backup generators. These features ensure that critical building systems, particularly life safety systems, can remain operational even if the main power source fails. The idea of integrating redundancy into critical systems is critical, but it does highlight the vulnerability of a structure of this size and height to potential disruptions in the power grid and other events.
Furthermore, the building includes specialized elevators specifically designed for firefighters to reach upper levels quickly during an emergency. This kind of foresight to aid rapid response shows a good understanding of emergency response needs in tall buildings. However, if a wider range of emergency scenarios were taken into consideration, it would be interesting to see how this design element could be further improved.
A thorough drainage system is implemented to deal with precipitation, protecting the building's integrity from water damage during heavy rains. It's clear that this aspect of the design was a significant consideration, given the structure's location and the potential for heavy rainfall. While the system seems well-designed, the ongoing effects of climate change with more frequent and severe rainfall patterns require careful review of the capacity and performance of the drainage system.
Lastly, comprehensive inspection and maintenance protocols are established for all safety equipment in the tower. This reflects an ongoing effort to ensure that emergency systems are ready for any potential hazards, reflecting the responsibility that comes with operating such an iconic structure. These rigorous processes are admirable, but the challenge of maintaining systems across 110 floors and dealing with components that will eventually age represents an area where further analysis and innovation could be explored.
The Engineering Marvel of Chicago's Willis Tower A Floor-by-Floor Analysis of its 110 Stories and Architectural Innovation - Building Movement Analysis How the Tower Sways 3 Inches in Chicago Winds
The Willis Tower's design incorporates a remarkable engineering solution to counter Chicago's strong winds: allowing the structure to sway. This intentional movement, up to three inches in windy conditions, is not a flaw, but rather a crucial component of its stability. The tower's 110 stories are subject to tremendous forces, and the ability to flex helps distribute the stress evenly. The "bundled tube" structure, a central aspect of the Willis Tower's design, plays a key role in both its height and wind resistance. While the concept of a swaying skyscraper might seem unusual, it's a testament to a creative engineering approach that enables the building to withstand strong winds. In a world where weather patterns are shifting, this design offers a fascinating example to analyze as we consider the challenges of building even taller and more resilient structures in the future.
The Willis Tower, a testament to structural innovation, is designed to handle the powerful winds common in Chicago. Its unique "bundled tube" design allows for a controlled sway of up to three inches at its peak during strong gusts. This intentional flexibility helps reduce stress on the tower's frame, a clever engineering solution that enables it to withstand the high-velocity winds.
To manage this movement, the tower incorporates tuned mass damper systems. These act as counterweights, adjusting dynamically to minimize sway and enhance the comfort of occupants. This sophisticated interaction between engineering and physics ensures the structure remains stable and safe in high winds, which can exceed 70 miles per hour on the upper floors.
The bundled tube system is integral to the building's ability to absorb and distribute wind forces. The interplay of the tubes, each with a distinct height, allows the tower to behave more like a flexible entity than a rigid one, minimizing oscillation and stress.
This thoughtful design extends to the 103rd floor's glass balconies, known as "The Ledge". These cantilevered structures are supported by multiple layers of laminated glass engineered to withstand both weight and the force of wind uplift. This is a fascinating example of how engineers can incorporate stunning design elements without compromising structural integrity.
While Chicago is not particularly prone to earthquakes, the tower's design still includes measures to withstand minor seismic events. Flexible connections allow the structure to absorb some seismic energy, a proactive step that showcases the engineers' understanding of potential threats to tall buildings.
Throughout the building, engineers took the variability of materials in mind, incorporating designs that accommodate thermal expansion and contraction of steel and glass. This attention to material behaviour under changing temperatures ensures structural integrity during weather extremes. Furthermore, advanced bracing systems minimize the sway experienced on the balconies and upper floors, demonstrating the architects' dedication to comfort and safety during extreme wind conditions.
The tower's emergency systems also include a robust network of wind sensors for real-time monitoring of wind speeds and direction. This allows for adjustments to maximize safety during high-wind events, showcasing a dynamic and adaptable design. The building features redundant safety features, such as dedicated elevators for emergency personnel. This proactive approach exemplifies a thorough understanding of the inherent challenges of maintaining a structure of this height and the importance of swift accessibility for emergency responders.
While the tower's innovative design successfully handles a variety of environmental forces, it's important to recognize that ongoing research and development could further refine the design and potentially enhance its response to various conditions. This iconic structure continues to be a remarkable example of how innovative engineering can not only overcome challenges but also create breathtaking design elements that benefit and awe people.
The Engineering Marvel of Chicago's Willis Tower A Floor-by-Floor Analysis of its 110 Stories and Architectural Innovation - Steel Frame Construction 76000 Tons of American Steel from Gary Indiana Mills
The construction of the Willis Tower relied heavily on a significant quantity of steel—a total of 76,000 tons—sourced from the Gary Works steel mill located in Gary, Indiana. This massive steel mill holds a prominent position within North America's steel industry, demonstrating both technological prowess and impressive output. Gary Works significantly contributes to Indiana's leading role in steel production, delivering the essential materials for architectural achievements like the Willis Tower. Utilizing local resources in the construction of the Willis Tower highlights the practicality and efficiency of steel frame construction while also emphasizing the area's industrial legacy. However, the social and economic implications associated with such large-scale steel production, including working conditions and environmental impact, warrant continued examination in the context of ongoing urban expansion. It's a reminder that while progress often relies on industrial contributions, a critical eye on the associated issues is paramount.
The Willis Tower's impressive 76,000-ton steel frame, largely sourced from the Gary Works mill in Indiana, showcases a fascinating blend of industrial heritage and modern engineering. This reliance on local steel minimized transportation costs and environmental impacts associated with material transport, highlighting the city's industrial roots. While the steel frame enabled the tower to soar into the Chicago skyline, the chosen bundled tube design surprisingly required less steel compared to conventional methods. This design choice emphasized structural efficiency, creating a relatively compact footprint while maximizing vertical reach.
The specific steel alloys used in the Willis Tower's construction deserve attention. They were selected to enhance strength and durability in Chicago's fluctuating temperatures, ensuring the building's long-term resilience against the harsh climate. The sheer weight of the steel frame during construction demanded a high level of scrutiny, with engineers continuously monitoring the foundation to prevent any settlement issues that could compromise the tower's structural integrity.
Interestingly, the steel frame design is engineered to absorb and disperse energy during high-wind events. The interaction between the frame and the building's overall mass allows for a controlled sway, minimizing occupant discomfort during windy conditions. The precision employed in joining steel beams was crucial, utilizing high-strength bolts and welds capable of withstanding dynamic forces encountered during strong winds or seismic events, reflecting the advancements in steel construction techniques.
Prior to construction, rigorous testing evaluated the bundled tube design against Chicago's renowned wind patterns using computational models. These simulations accurately predicted the tower's behavior under different wind conditions, ensuring stability during severe weather. Each of the nine tubes forming the tower's core not only contributes to its aesthetic but also plays a key role in distributing vertical loads. This design smartly balances stress across the structural elements, allowing for redundancy and overall stability.
Steel's inherent thermal properties posed challenges for the tower's design, particularly concerning thermal expansion and contraction in varied temperatures. The engineers expertly addressed this by incorporating thermal joints into the steel frame, maintaining structural integrity under various temperature conditions. Modular construction techniques were also employed, allowing for prefabrication of large sections of the steel frame off-site. This expedited construction time on-site and reflected advancements in manufacturing technology, exemplifying how improved processes can optimize urban construction projects. While innovative, one can't help but wonder if these practices could have been further refined or perhaps alternative materials explored for potentially even greater efficiency or resilience.
More Posts from urbanplanadvisor.com: