How China's CR400AF-G Reached Record-Breaking 435 km/h in Latest High-Speed Rail Tests
How China's CR400AF-G Reached Record-Breaking 435 km/h in Latest High-Speed Rail Tests - CR400AF-G Sets 435 km/h Speed Record During April 2024 Puyang Trial Run
During trials in Puyang in April 2024, the CR400AF-G, a model within China's Fuxing high-speed train family, reached an impressive top speed of 435 km/h. This marked a significant advancement beyond its usual operational speed of 350 km/h, demonstrating the continuous development of high-speed rail technology in the country. The train's design incorporates over 2,500 monitoring points, allowing for real-time assessment of various components and conditions, which are crucial for ensuring the train's safety and performance. While this speed record underscores the potential of China's high-speed rail, it also necessitates a careful evaluation of the associated safety and infrastructure requirements needed to support such high speeds. The CR400AF-G's capacity to operate reliably in frigid environments, even as low as -40°C, makes it a potentially versatile model for a country with a wide range of climatic conditions.
Reaching 435 km/h, a speed achieved by the CR400AF-G during its April 2024 trial run in Puyang, required careful track preparation. The trial route was specifically designed, considering gradient, curve radius, and track banking to ensure stability at such high speeds and minimize air resistance. This highlights that simply increasing engine power isn't enough - the entire rail environment needs optimization for truly high-speed operation.
Extensive simulations preceded the physical trial run. Researchers had to estimate the potential effects of factors like temperature changes and wind resistance on the CR400AF-G's structure. This rigorous testing aimed to ensure the train could handle the stress imposed at these extreme velocities. It seems they have taken a more systematic approach compared to some of their earlier projects.
The CR400AF-G's aerodynamic design is undoubtedly significant in reaching such speeds. A streamlined front and body help reduce air resistance (drag). This is especially important when a train tries to exceed the 400 km/h mark. These design features, coupled with the active suspension system, were critical in this record run.
Speaking of the suspension, it's noteworthy that the CR400AF-G uses active suspension, which dynamically adapts to varying speed and track conditions. This is fascinating as it improves both passenger comfort and safety at these high velocities. It would be insightful to study the specifics of the control algorithms and the actuator systems used for this adaptive suspension.
During the Puyang trial, the train’s performance was meticulously monitored. Engineers collected a wealth of real-time data under extreme conditions. This data, I'm sure, will inform future improvements to high-speed rail technology. It makes me wonder what improvements they have already incorporated after evaluating the April data.
A significant aspect of the CR400AF-G is its reliance on materials like lightweight alloys and composites. These materials contribute to achieving a strong yet lightweight structure, which is essential to reaching high speeds. It would be interesting to review the specific materials employed in the CR400AF-G compared to other models within the Fuxing family and understand the implications of material selection on high-speed performance.
Predictive modeling techniques played a crucial role in this high-speed project. By using these methods, engineers could anticipate potential mechanical issues during the test runs. It underlines how reliant these high-speed endeavors are on data analytics. Perhaps predictive models can help reduce the number of physical tests needed in the future.
Safety was of course paramount, as with any high-speed rail project. The Puyang trial implemented careful safety protocols, including automated emergency braking systems. This is essential given the potential consequences of failures at 435 km/h. It is reassuring to know that safety precautions are incorporated for a system that is, to a certain extent, still being proven in practice.
This 435 km/h speed record clearly positions the CR400AF-G amongst the fastest commercial trains. However, it also brings critical questions into focus. Can the infrastructure handle the sustained operation of trains at such speeds? What are the maintenance implications for these systems? I think this warrants further investigation.
The CR400AF-G project shows a continued pursuit of high-speed rail with a focus on energy efficiency. Balancing speed with operational costs is a key challenge in modern high-speed rail design. Understanding the energy consumption at these speeds and the efficiency of the distributed power systems becomes especially important for the viability of this technology in the long run. Is it possible to reduce the energy intensity while continuing to develop higher speed trains? This is another area to explore.
How China's CR400AF-G Reached Record-Breaking 435 km/h in Latest High-Speed Rail Tests - Engineering Behind China's New Train Brake and Suspension System
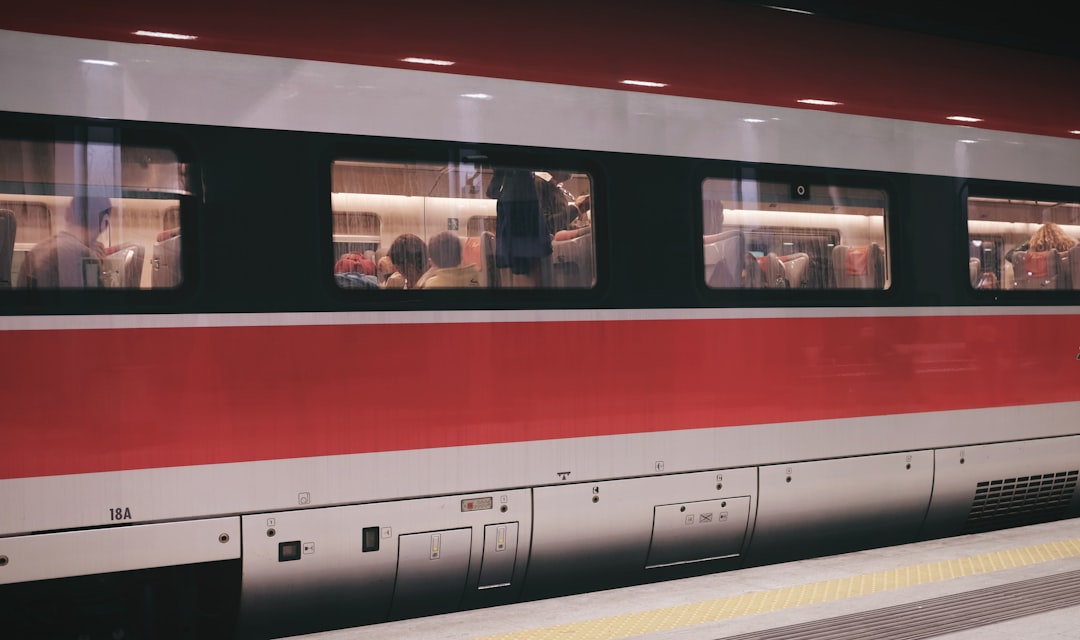
The CR400AF-G's ability to reach 435 km/h hinges on several engineering feats, particularly in its braking and suspension systems. The active suspension is a key element, constantly adapting to changes in track conditions and speed. This dynamic adjustment contributes to a smoother ride and enhances stability, crucial for safety at such high speeds. The train's structure also benefits from the use of lightweight, yet strong materials. This reduces the overall weight, making it easier to achieve high velocities and minimizing energy consumption. Furthermore, engineers utilized a more rigorous approach to design, incorporating extensive predictive modeling to anticipate potential mechanical failures. This focus on simulation and analysis shows a more advanced approach to developing high-speed rail systems. It seems the team has learned from past projects and improved the planning stages considerably. These enhancements to braking and suspension, alongside the sophisticated design process, highlight a significant step forward in China's high-speed rail engineering capabilities. While the implications for maintenance and wider infrastructure are still areas of inquiry, these innovations suggest a promising future for even faster, more efficient rail travel.
The engineering behind the CR400AF-G's brake and suspension systems is fascinating. It utilizes a distributed braking system that incorporates regenerative braking, a clever way to convert the train's kinetic energy into electrical energy during deceleration. This enhances braking efficiency and potentially improves overall energy efficiency. It's interesting how this system is integrated with the 2,500 monitoring points to potentially allow for advanced collision avoidance technology.
Another aspect I find compelling is the electronic control of the suspension. Sensors constantly monitor the track conditions and adjust the stiffness and damping characteristics of the suspension components. This dynamic adaptability is crucial for keeping the train stable at high speed and, of course, for enhancing passenger comfort.
It's clear that accommodating these advanced systems required changes to the track infrastructure. The track designs have been optimized with aspects like cant and cross-profile to reduce the lateral forces on the train, enhancing safety and ride quality. The use of composite materials in the suspension components is also interesting. By using lighter but strong materials, they can reduce weight without sacrificing strength, which is vital when trying to reach such high speeds.
High-speed operation generates a considerable amount of heat, especially in the braking system, so it's no surprise the CR400AF-G has advanced thermal management systems. These are essential to maintain the brake's performance, especially during prolonged use at extreme speeds. The inclusion of aerodynamic braking alongside traditional brakes also intrigues me. It leverages air resistance, reducing reliance on the physical brakes and extending their lifespan.
Of course, safety is paramount at these speeds. Fail-safe mechanisms are essential. Having redundant braking systems that automatically engage in case of a primary system failure is reassuring. This is critical, as the consequences of failure at 435 km/h would be severe.
It's also notable that engineers are carefully analyzing how gradients affect braking efficiency and overall speed. Understanding this aspect is key for route planning and ensuring optimal train performance without compromising safety. The sheer amount of data collected during these trials is also significant. It allows for very detailed post-test analysis, which will undoubtedly feed into future designs and improvements. Aspects like brake wear, suspension behavior across speeds, and aerodynamic performance can be carefully studied to make gradual improvements to high-speed rail technologies.
Overall, it seems the CR400AF-G represents a significant leap forward in high-speed train engineering. The careful consideration of braking efficiency, suspension design, safety, and material selection showcases a serious approach to technological development. It will be very interesting to see how these lessons learned will impact future iterations of high-speed rail projects in China and globally.
How China's CR400AF-G Reached Record-Breaking 435 km/h in Latest High-Speed Rail Tests - Dual Train Test Achieves 870 km/h Relative Speed on Jinan Railway
Recent trials on the Jinan Railway have demonstrated impressive high-speed rail capabilities, achieving a relative speed of 870 km/h during a dual-train test. This remarkable speed was achieved when two CR400AF trains, each traveling at 435 km/h, passed each other. This achievement represents a significant advancement in high-speed rail technology, particularly in the context of the CR400AF, a train part of the domestically-developed Fuxing series. The tests, which set new speed records for both open tracks and tunnels, emphasize the considerable engineering efforts and innovative technologies incorporated into these trains.
While this success highlights the potential of China's high-speed rail system, it also raises pertinent questions concerning the implications of such high speeds. Can existing and planned infrastructure adequately support consistent, high-speed operations? How will the required safety protocols evolve to manage the risks associated with these increased speeds? The expansion of China's high-speed rail network, already the world's longest, compels a thorough re-evaluation of operational standards and safety measures as the country pursues faster and more efficient transportation. It will be interesting to see how the insights gained from these record-breaking trials influence future designs and infrastructure developments.
During trials on the Jinan-Zhengzhou high-speed railway, two CR400AF-G trains traveling in opposite directions achieved a remarkable relative speed of 870 km/h. This represents a new benchmark for high-speed rail, demonstrating the potential for exceptionally fast travel when considering the combined speeds of multiple trains. It is a notable achievement, though the practical implications of such speeds need further consideration.
Coordinating two trains at such high velocities presented a unique engineering challenge. Keeping them on a precise schedule and avoiding any potential collisions required incredibly detailed control algorithms and careful planning. This highlights that high-speed rail isn't simply about engine power – it involves intricate systems for safe and synchronized operation.
The streamlined designs of both trains played a pivotal role in minimizing air resistance, which becomes a significant hurdle at speeds approaching 435 km/h. This design optimization is crucial to achieving and sustaining such high speeds. It appears that researchers used detailed computational fluid dynamics simulations prior to the test to refine the trains’ shape and predict airflow patterns. This advanced approach aims to reduce turbulent air flows that might lead to instability, showcasing a commitment to detailed engineering before physical testing.
It's evident that track conditions heavily influence high-speed rail performance. The Jinan section underwent substantial upgrades to its alignment and foundation to ensure stability at such high speeds. This highlights the interconnectedness between track infrastructure and the train itself – building fast trains isn't enough; the tracks must be equally well-developed to support such high speeds.
During the trials, extensive safety measures were incorporated. Each train was equipped with sophisticated sensor systems capable of real-time speed and distance monitoring, integrating with automatic emergency braking mechanisms. This is essential at speeds of 435 km/h, where any deviation could have significant consequences. It will be interesting to study the specifications and sensitivity of those sensors.
The high relative speed also created considerable electromagnetic fields, requiring additional measures to prevent interference with the trains' onboard systems. This illustrates the complex interactions between components, especially at high speeds. The challenges in this area may indicate potential limitations to increasing train speeds further.
This success raises questions about how the infrastructure can support sustained, high-speed operation. It's essential to determine how such extreme dynamic forces affect the long-term durability of the track and other components over time. It's also critical to evaluate what the maintenance costs would be for such systems.
The data gathered from this high-speed dual-train test will be instrumental in refining predictive maintenance models. By analyzing the wear patterns and potential fatigue in both the trains and the track under these extreme conditions, engineers gain crucial insights into system performance. Understanding this aspect better should improve future designs and potentially reduce the need for some physical tests.
The 870 km/h relative speed achievement may spark further investigation into aerodynamic drag reduction strategies. This emphasizes the continued need for innovation in the materials and design approaches to high-speed rail technologies. Perhaps, lighter, more advanced materials or refined aerodynamic shapes are needed to improve efficiency at higher speeds. This points to a future where these technologies are continuously improved.
How China's CR400AF-G Reached Record-Breaking 435 km/h in Latest High-Speed Rail Tests - Safety Upgrades From 2011 Train Standards to Current CR400AF Design
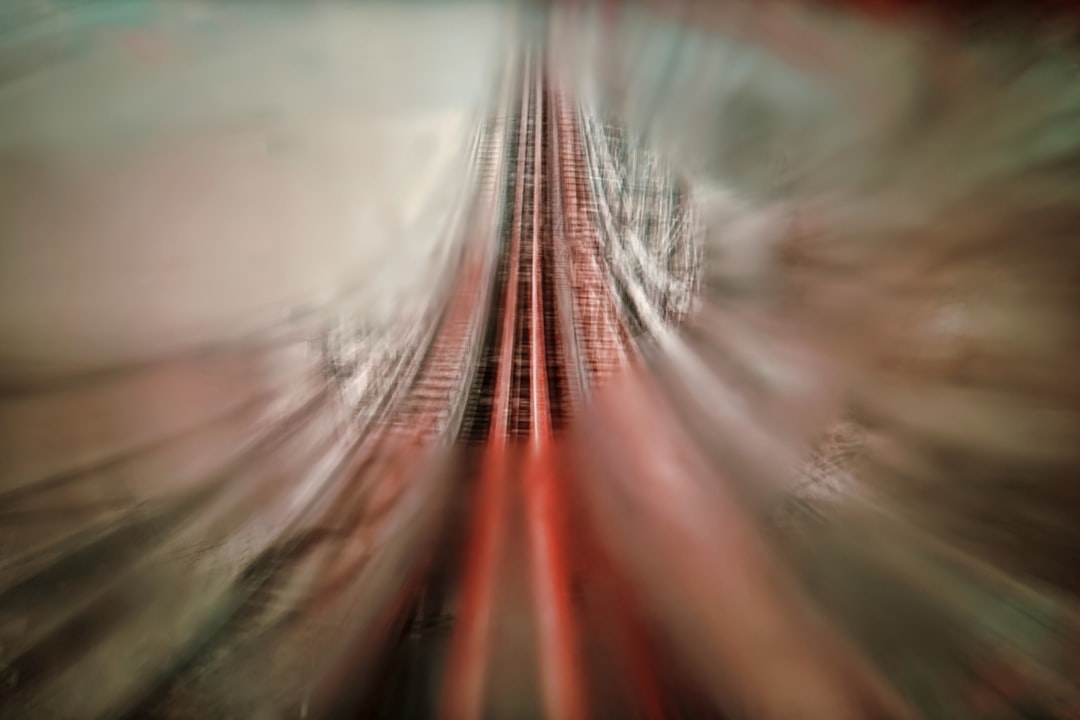
The CR400AF design represents a substantial advancement in safety compared to the 2011 train standards. It boasts a comprehensive suite of monitoring systems, utilizing over 2,500 data points to provide real-time insights into the train's status and its surrounding environment. This constant stream of information aids in immediate identification and potential mitigation of any emerging issues.
Furthermore, the CR400AF incorporates a more sophisticated braking system, including regenerative braking, which improves energy efficiency and braking performance. Active suspension technology has also been integrated to dynamically adapt to varying speed and track conditions. This active suspension not only improves ride comfort but plays a crucial role in enhancing the overall stability of the train at higher speeds, contributing to increased safety.
Beyond the core braking and suspension systems, advancements in thermal management and aerodynamic design have been integrated into the CR400AF. These improvements are critical for managing the increased heat generated at high speeds and for reducing drag at extreme velocities. These elements work together to significantly reduce the inherent risks of high-speed travel.
The incorporation of these technologies demonstrates a greater emphasis on safety in modern high-speed rail designs, aligning with the escalating performance and speed capabilities of trains like the CR400AF. While these advancements are promising, it's essential to remember that continuous evaluation and improvement of safety protocols are required as train speeds continue to increase.
The evolution from the 2011 train standards to the current CR400AF design represents a significant leap in safety and performance. One key advancement is the integration of a far more comprehensive monitoring system. The CR400AF utilizes over 2,500 sensors that provide real-time data on the train's structure, track conditions, and mechanical components. This represents a huge improvement over the previous generation, which relied on a much smaller number of monitoring points.
The braking systems have also seen a major overhaul. The CR400AF-G incorporates a distributed braking system with regenerative capabilities. This allows it to convert a substantial portion of the train's kinetic energy into electrical energy during deceleration, enhancing efficiency and reducing reliance on traditional brakes. This is a far cry from the predominantly conventional braking systems found in 2011-era designs.
The move to active suspension is another noteworthy development. In contrast to the static suspension systems of older trains, the CR400AF's active suspension constantly adapts to track conditions and speed. This not only enhances ride comfort but also contributes to greater stability at high speeds by minimizing lateral forces.
Interestingly, the CR400AF design places a strong emphasis on thermal management. The advanced braking systems generate considerable heat, which necessitates sophisticated cooling systems to ensure optimal performance. This attention to thermal dynamics is indicative of a greater understanding of material properties and heat transfer than was present in previous high-speed rail designs.
The shift to higher-strength, lightweight materials like alloys and composites is also a key aspect. These materials provide a strong yet lightweight structure, crucial for achieving and maintaining high speeds. They also exhibit improved fatigue resistance compared to materials used in older trains, which were less suited to the stresses encountered at such high velocities.
Furthermore, the CR400AF incorporates electromagnetic interference shielding in its design. This is essential considering the significant electromagnetic fields generated during high-speed operation. This addition tackles a potential issue that earlier designs hadn't adequately considered, highlighting a more integrated and sophisticated approach to technology integration.
Another noteworthy feature is the incorporation of sophisticated predictive maintenance algorithms. The CR400AF's system continuously analyzes real-time data to anticipate wear and fatigue, enabling more proactive maintenance practices. This is a major shift from the more reactive maintenance approach prevalent in the trains built under the 2011 standards.
It's clear that the CR400AF design has undergone significant aerodynamic and track optimization. The design incorporates track specifications, such as banking and curvature, specifically tailored for high-speed dynamics. In comparison, the previous standards didn't fully account for the intricate interplay of aerodynamic and gravitational forces at high speeds.
Operationally, the CR400AF employs an advanced communication system that enhances coordination between multiple trains, reducing the risk of collisions at high speeds. This represents a considerable improvement over the less sophisticated safety mechanisms employed in the past.
Finally, safety standards have been significantly enhanced. Advanced automated emergency systems can intervene in real-time to mitigate potential hazards at extremely high speeds. These systems are far more complex and responsive than their 2011 counterparts, a crucial aspect considering the inherent risks associated with operating trains exceeding 400 km/h.
In conclusion, the evolution from the 2011 train standards to the CR400AF design is marked by numerous advancements in safety, monitoring, and overall technological sophistication. This progress provides a clear roadmap of the evolution of high-speed rail engineering in China. However, the ongoing challenge of ensuring that infrastructure and maintenance procedures can adequately support sustained high-speed operations remains critical for the widespread adoption of such cutting-edge technology.
How China's CR400AF-G Reached Record-Breaking 435 km/h in Latest High-Speed Rail Tests - Nine Indigenous Technologies That Power the CR400AF Locomotive
China's CR400AF locomotive represents a significant stride in the country's pursuit of self-sufficient high-speed rail technology. It incorporates nine domestically-developed technologies that are central to its performance and efficiency. Among them are a high-power traction system designed to be both lightweight and highly efficient, showcasing a noteworthy power density increase compared to older models. The train is meticulously monitored through a network of over 2,500 data points, allowing engineers to track real-time conditions and predict potential maintenance needs. An innovative active suspension system dynamically adapts to changing track conditions and speeds, enhancing both passenger comfort and train stability, particularly at high speeds.
Furthermore, the CR400AF exemplifies the integration of advanced technologies into train operations. It leverages cloud computing, big data, and even 5G connectivity to improve efficiency and decision-making. This shift towards a more digitally-integrated approach is apparent in the proactive maintenance strategies and intelligent operations facilitated by these systems. The CR400AF showcases China's ambition to not only design and build its own high-speed trains but also to control and advance the underlying technologies that support them. This move away from relying on foreign technologies signals a broader engineering shift and sets the stage for future advancements in the field. While the focus on domestic technology development is apparent, it's crucial to consider the longer-term implications of this strategy, including issues surrounding infrastructure and maintenance, and the costs associated with maintaining this sophisticated technology.
The CR400AF, a product of China's domestic high-speed rail development, incorporates several noteworthy indigenous technologies. Its construction uses advanced alloys and composites, resulting in a lighter yet stronger structure compared to earlier designs. This weight reduction is pivotal for achieving and sustaining high speeds.
The train's active suspension system is a remarkable feat of engineering. Not only does it adjust to changes in speed, but it also dynamically adapts to imperfections in the track, leading to a smoother ride for passengers and greater stability at high velocity. This is crucial in mitigating risks associated with very fast travel.
Another fascinating aspect is the inclusion of a regenerative braking system. This system can convert a significant portion of the train's kinetic energy into electricity during braking, potentially reducing energy consumption and extending the lifespan of traditional brakes. It's worth exploring how effective this conversion actually is in practice.
The CR400AF is equipped with over 2,500 monitoring points that continuously assess its structural integrity and mechanical health. This abundance of data provides an opportunity to implement predictive maintenance strategies and anticipate potential issues before they develop into critical failures. It's certainly an ambitious approach, but it remains to be seen how effective it proves in the field.
Operating at these speeds generates substantial electromagnetic interference, a factor that previous generations of high-speed trains didn't adequately address. The CR400AF implements specialized shielding to minimize this issue. It's interesting to wonder how robust this shielding actually is and whether there are limitations to what can be accomplished with current technology.
The CR400AF's shape was carefully designed through computational fluid dynamics simulations, which helps in reducing aerodynamic drag, a crucial factor in maintaining high speeds. It's a complex challenge, and I wonder if more could have been done in this area given the technology available.
In the realm of safety, the train incorporates advanced emergency braking systems. These systems can react instantly to anomalies, a marked improvement over the less reactive systems of older trains. One question arises about the level of autonomy in these systems and how they can be effectively verified.
Managing the considerable heat generated at high speed is achieved through innovative thermal management systems. These systems aim to prevent overheating of braking components and ensure consistent performance. How these systems cope with different climatic conditions is an area I believe merits further scrutiny.
To optimize the CR400AF's performance, the supporting rail infrastructure has undergone significant upgrades. This includes enhancements to the alignment and foundation to withstand the dynamic forces at very high speeds. The effectiveness of these modifications and their longevity will be critical to the viability of high-speed rail at these levels.
Lastly, the intricate coordination of the dual-train test at a combined speed exceeding 870 km/h required sophisticated control algorithms to avoid collisions and maintain a strict schedule. It is a testament to the complex engineering challenges of high-speed rail systems. It will be interesting to see how these algorithms evolve with future testing and development of the CR400AF and similar projects.
These technologies represent a significant step forward in China's high-speed rail capabilities, showcasing their ability to develop indigenous solutions. However, the long-term implications for maintenance, infrastructure durability, and the widespread adoption of these high speeds warrant continued research and evaluation.
How China's CR400AF-G Reached Record-Breaking 435 km/h in Latest High-Speed Rail Tests - Temperature Adaptations for Extreme Weather Operations From Beijing to Shanghai
China's high-speed rail network, particularly the routes between cities like Beijing and Shanghai, faces increasing challenges from extreme weather. The CR400AF-G has been engineered with a focus on adapting to these harsh climatic conditions, operating effectively across a wide temperature range, from frigid -40°C to sweltering summer heat. This capability is becoming increasingly vital as China experiences more frequent and intense weather patterns, as demonstrated by recent temperature spikes in cities such as Beijing, where readings exceeded 41.8°C. The anticipation of even greater climate change-induced temperature extremes in the future underlines the importance of continuous advancements in train design, as well as operational strategies. Maintaining high-speed rail's efficiency and safety in the face of such variable weather will be a crucial aspect of expanding and maintaining this vital transportation infrastructure. It remains to be seen how effectively these adaptations will function in real-world operational scenarios, especially during extended periods of extreme heat or cold.
The CR400AF-G is engineered to operate across a wide temperature range, from -40°C to 40°C, a testament to its adaptability to China's diverse climate. This broad operational temperature window requires specialized thermal management systems and materials. Engineers have focused on using innovative materials and insulation to ensure critical electronic components function flawlessly even in extreme conditions. For passenger comfort and system efficiency, it incorporates sophisticated air conditioning systems utilizing heat exchangers to effectively manage temperature variations, especially crucial in regions like Beijing and Shanghai, which experience significant temperature swings throughout the year.
Each CR400AF-G has built-in self-diagnostic features that monitor the temperature of critical components in real-time. This constant monitoring helps anticipate and potentially prevent failures before they occur, showing a shift toward proactive maintenance driven by temperature data. Furthermore, it’s equipped with thermal imaging cameras that continuously scan track conditions. This advanced feature allows engineers to identify heat-induced deformations in the rails that might occur due to extreme temperature changes.
The importance of rail geometry adjustments cannot be overstated when designing for high-speed operation. As temperatures fluctuate, rails expand and contract, potentially impacting track alignment. The CR400AF-G addresses this by running on specially engineered tracks that incorporate expansion joints to account for thermal changes. Also, its wheel-rail interface employs low-friction materials. These materials, besides enhancing performance, reduce wear and tear, contributing to extended maintenance intervals.
The CR400AF-G's active suspension system is intricately designed to adapt to temperature fluctuations. Its sensors gather real-time temperature data and adjust the suspension characteristics to maintain optimum stability and passenger comfort. This adaptive capability is impressive and shows a level of sophistication in the train's control strategies. Regarding safety, emergency procedures are designed with extreme weather in mind. For example, the train's systems can automatically adjust operating thresholds, such as reducing speed when severe weather conditions are detected.
When designing the CR400AF-G's aerodynamic profile, simulations factored in the effects of thermal changes on airflow patterns. Since heat affects aerodynamic performance at high speeds, a thorough understanding of this interaction was essential. This detailed approach likely contributed to its aerodynamic efficiency and ability to reduce drag at high speeds.
The CR400AF-G's electrical systems are meticulously designed to withstand thermal variations. The engineers have included redundant systems and thermal insulation to prevent overheating, particularly during prolonged operation in extreme conditions. This emphasis on robustness indicates an awareness of the challenges posed by operating high-speed trains in the face of increasingly extreme weather.
While the CR400AF-G seems to represent a leap forward in high-speed rail engineering, it is crucial to understand the interplay between design, materials, and real-world operation. It will be interesting to see how these adaptations perform in various weather conditions and the overall operational impact of the temperature management systems during extended periods of operation.
More Posts from urbanplanadvisor.com: