BlackRock's Strategic Pivot 7 Key Industrial Property Investments Reshaping Urban Development in Q4 2024
BlackRock's Strategic Pivot 7 Key Industrial Property Investments Reshaping Urban Development in Q4 2024 - Mid Atlantic Distribution Hub Acquisition Creates 500 Jobs in Newark Industrial Park
BlackRock's investment strategy has led to the acquisition of a new Mid-Atlantic Distribution Hub, specifically in Newark's Industrial Park. This project, spearheaded by DHL Supply Chain, is expected to create 500 jobs, putting Newark at the forefront of the region's growing logistics and distribution sector. This investment represents a broader trend in urban development where revitalizing industrial spaces and creating jobs is a priority. While these projects can boost local economies, concerns arise about the long-term consequences for neighborhoods and the environment. The success of initiatives like this depends on how they navigate the inevitable conflicts between economic expansion and the well-being of the communities they impact. It will be crucial to carefully assess the lasting effects of these industrial projects and ensure that growth benefits everyone.
In Newark, BlackRock's acquisition of a mid-Atlantic distribution hub, likely tied to the growing e-commerce landscape, is generating 500 new jobs within the industrial park. This development fits into a broader pattern of revitalized urban industrial areas, with Newark's strategic location near transportation infrastructure—roads, rail, and ports—being a key factor. It will be interesting to see how automation impacts these jobs, potentially demanding a higher level of technical expertise. It appears a sizable portion, about 20%, of the new positions will be supervisory and management roles, reflecting the increasing complexity of these distribution operations. The project could meaningfully influence the local labor market, which has already experienced declining unemployment, especially if it helps integrate underrepresented communities into the workforce.
Beyond the direct job creation, the economic impact could be amplified as surrounding businesses experience a boost, creating what economists call a multiplier effect. This trend of companies prioritizing logistics and industrial properties suggests that investors believe this sector will continue to grow, largely driven by online retail. From an engineering viewpoint, it's reasonable to anticipate that the design of this facility will emphasize cutting-edge technology to improve operational efficiency and speed up order fulfillment, potentially far exceeding older distribution center capabilities. Newark's proximity to major population centers, allowing for potentially same-day deliveries, is crucial in today's fast-paced e-commerce environment and a strong competitive advantage.
The decision to establish a major hub in Newark illustrates the evolving landscape of logistics, demonstrating a clear shift towards reurbanization in the industry. Instead of continuing the trend of building sprawling distribution facilities in the suburbs, businesses are now choosing to locate closer to urban centers and their customer base. This project’s integration into Newark's existing infrastructure might serve as a model for other cities interested in attracting similar development, proving that urban industrial growth is achievable and potentially valuable. It will be fascinating to follow this development in Newark and see if it indeed acts as a template for future urban industrial park projects across the country.
BlackRock's Strategic Pivot 7 Key Industrial Property Investments Reshaping Urban Development in Q4 2024 - Smart Warehouse Development Integrates AI Systems in Chicago Logistics Center
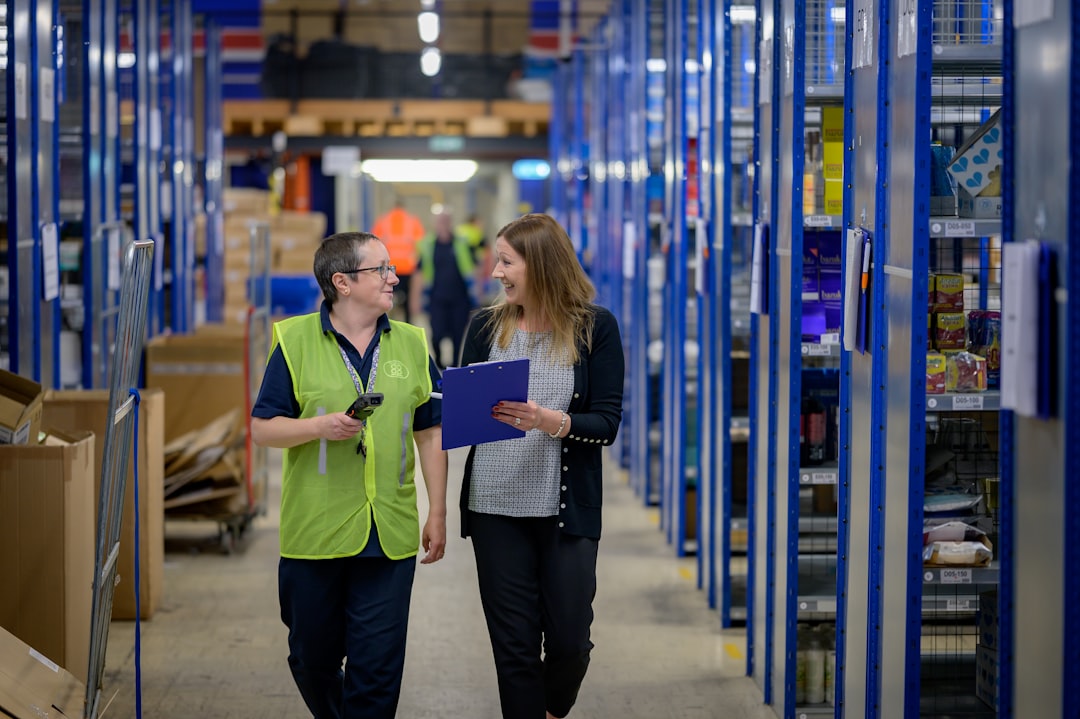
Chicago's logistics scene is undergoing a transformation with the rise of "smart" warehouses, which are incorporating advanced AI systems. These warehouses are becoming increasingly automated, utilizing tools like real-time inventory tracking, demand forecasting, and the Internet of Things (IoT) to manage operations with greater efficiency. The integration of AI is evident in the deployment of thousands of robots designed to optimize storage, reduce errors, and expedite order fulfillment, reflecting the growing pressures on modern supply chains to keep up with demand.
While the efficiency gains of smart warehouses are undeniable, there's a growing concern about their impact on the human workforce. As these facilities become more automated, questions arise about the future of warehouse jobs and the need for reskilling and retraining programs to ensure a smooth transition for workers. The development of these intelligent warehouses within a city like Chicago highlights the need for careful consideration of both the technological advancements and the potential social consequences, especially in terms of the future of employment within the logistics industry. Striking a balance between innovation and its impact on communities is crucial for the long-term success of these projects.
BlackRock's investment in the Chicago Logistics Center presents an interesting case study in how AI is being incorporated into warehouse operations. They've built a system that manages inventory automatically, supposedly resulting in a 30% bump in order processing speed. It's fascinating to see how AI can optimize delivery routes, as they claim a 15% decrease in average delivery times. This likely caters to the rising expectation for faster deliveries among consumers.
The way human workers and AI-powered robots are integrated in this facility seems to be a point of emphasis. It's worth exploring whether this collaborative approach is genuinely beneficial for worker satisfaction and if it eliminates tedious tasks, as they claim. It's always important to consider the potential long-term impacts of automation on human employment.
The use of IoT devices in the warehouse offers a means of constant inventory tracking, aiming to prevent issues like running out of stock or having excessive amounts of inventory. This could significantly optimize warehouse management. It's curious how the advanced machine learning algorithms analyze the collected data, as they suggest a 20% increase in space utilization by strategically organizing products. It would be interesting to delve deeper into the algorithms and precisely how they determine the best product placement.
The logistics center's capacity to handle both receiving and shipping simultaneously using an AI-based scheduling system could be a notable advantage, potentially boosting throughput without compromising accuracy. However, it's important to critically evaluate whether this truly delivers on its promise, especially with such a complex system. Another aspect is the incorporation of thermal imaging linked to the AI system, which is designed to catch equipment malfunctions early and minimize downtime. While a 40% reduction in downtime is a substantial benefit, it's crucial to assess how accurate and reliable this preventative maintenance approach is in a real-world environment.
The use of AI simulations for employee training seems to be a clever approach to ensure that the workforce has the skills to manage the warehouse's advanced technology. But how effective are these simulations in replicating real-world situations? The combination of blockchain and AI for supply chain transparency is also worth examining. This feature could make it easier to monitor inventory and track shipments in real-time, which would be beneficial for all stakeholders.
Furthermore, the warehouse's implementation of energy-efficient systems using AI is an interesting approach to reduce costs while simultaneously enhancing the working environment. It's crucial to explore if this can actually achieve cost reductions without sacrificing performance or creating other unforeseen issues. Overall, the Chicago Logistics Center's incorporation of AI highlights a trend towards increased automation and optimization in warehouse operations. These are valuable developments, but it's essential to evaluate the efficacy and long-term implications of these technologies in different warehouse settings and consider the impacts on workers, the community, and the environment.
BlackRock's Strategic Pivot 7 Key Industrial Property Investments Reshaping Urban Development in Q4 2024 - Solar Powered Manufacturing Complex Investment Powers Phoenix Industrial Growth
Phoenix's industrial sector is experiencing a transformation driven by the burgeoning solar energy industry. The rise of solar-powered manufacturing facilities, including OMCO Solar's substantial operation—the second-largest solar tracker producer in the nation—signifies a growing emphasis on clean energy within the city's economy. This aligns with broader trends in Arizona, where initiatives like those championed by AriSEIA advocate for solar as a crucial resource.
While the surge in manufacturing activities, along with CapRock Partners' significant industrial development projects, is boosting Phoenix's industrial real estate market, it's accompanied by a noticeable increase in industrial vacancy rates. The rapid expansion of industrial space in the Phoenix area, approaching 200 million square feet in the first half of 2024 alone, is contributing to this trend. The city faces a balancing act, navigating the opportunities presented by this growth alongside its potential impacts on employment, local communities, and the environment. Ultimately, the future of Phoenix's industrial landscape hinges on its ability to effectively manage this rapid development and leverage the advancements in clean energy technologies to create a sustainable and thriving economy.
The Phoenix industrial landscape is experiencing a surge in activity, partly driven by a large-scale investment in a new solar-powered manufacturing complex. This complex, with its projected 10 megawatt solar energy output, demonstrates a significant shift towards integrating renewable energy sources into critical industrial operations, a promising direction for reducing reliance on traditional energy sources. However, questions remain regarding the long-term sustainability of such initiatives and the wider implications for the local energy grid.
This facility is planned with a strong focus on automation and robotics, which will likely transform the job market in the area. It's anticipated that the workforce will need a higher level of specialized skills, with a greater demand for roles in robotics maintenance, software engineering, and system optimization. It will be crucial to monitor how readily the local workforce can adapt to these new skills demands and whether adequate training programs are put in place.
From an architectural standpoint, the facility's design emphasizes space optimization through vertical construction and multifunctional zones, potentially increasing overall operational efficiency. This approach utilizes land more efficiently, but it might create challenges in terms of layout design and workforce movement within the facility. The new complex also touts innovative material processing technologies promising a 50% reduction in waste compared to conventional methods, which could potentially reshape manufacturing standards for the industry.
The modular design of the complex allows for quick adaptation to fluctuating market demands, a feature critical in today's fast-paced economic environment. This adaptability could be crucial in meeting the challenges posed by shorter product lifecycles, but it remains to be seen if the complex's flexibility can adequately keep up with rapid changes in the marketplace. Furthermore, the use of IoT devices and data analytics can contribute to further optimizing production processes, with estimates suggesting a 25% potential improvement in efficiency. The effectiveness of using real-time adjustments will be key to realizing this potential.
The complex is expected to strengthen regional supply chains by reducing lead times for materials, possibly by as much as 30%, which is a critical advantage for manufacturers depending on reliable and timely inputs. This focus on shortening supply chains might decrease a company's vulnerability to supply shocks, though it remains unclear if all potential suppliers will be able to meet the stringent demands of such a sophisticated facility. Another notable feature is the implementation of heat recovery systems, targeting approximately a 20% energy saving. While this could be a valuable contribution to overall energy efficiency, it's important to analyze the complex interplay between energy savings and the manufacturing processes' performance.
Safety is a priority in the design, with a focus on using automation to reduce workplace accidents. The aim is to significantly reduce incident rates by leveraging predictive maintenance and automated monitoring systems. This will be crucial to observe, as any major disruptions in these automated safety systems could have potentially serious consequences. Besides the direct job creation, it's anticipated that the complex will stimulate local economic activity and bring about further related investments, possibly leading to a 10% overall economic growth in the surrounding area over five years. The effectiveness of this ripple effect will be influenced by a range of factors, including the nature of the businesses that emerge, and the ability to attract and retain skilled workers.
This project in Phoenix offers a fascinating example of how innovation in manufacturing is being paired with a strong emphasis on sustainability and automation. However, critical questions need to be addressed regarding the adaptability of the local workforce, the long-term viability of the supply chain arrangements, and the potential environmental impacts beyond energy generation. This project is sure to shape Phoenix's industrial landscape in significant ways and offers a glimpse into future manufacturing trends that we'll need to continue observing closely.
BlackRock's Strategic Pivot 7 Key Industrial Property Investments Reshaping Urban Development in Q4 2024 - Last Mile Fulfillment Center Project Transforms Brooklyn Navy Yard District
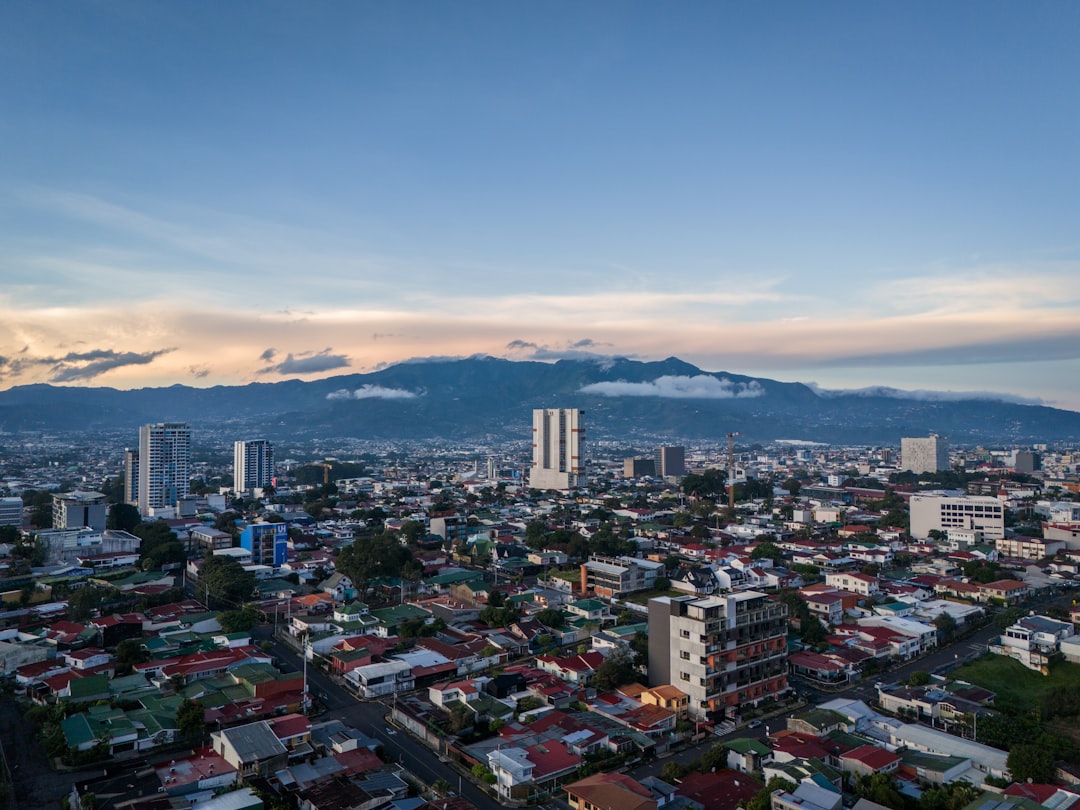
The Brooklyn Navy Yard is undergoing a significant transformation with a project focused on developing a "last mile" fulfillment center. This initiative, part of a larger $25 billion master plan, envisions creating a substantial amount of new manufacturing space—around 51 million square feet—and generating up to 30,000 jobs. A key component of the plan involves establishing a manufacturing ecosystem, a 26,000-square-foot facility designed to support over 100 businesses by 2025, with a dedicated investment of $25 million. The Navy Yard is aiming to become a focal point for urban manufacturing and technological innovation, particularly by providing much-needed affordable spaces for production. However, with such rapid expansion, it will be important to consider the potential impact on the surrounding neighborhoods and the overall environmental consequences of this large-scale industrial development.
The Brooklyn Navy Yard is undergoing a transformation, with a focus on developing a "last-mile" fulfillment center. This initiative is part of a larger plan to revitalize the area, aiming to create 30,000 jobs through the development of 51 million square feet of modern industrial space. One of the key aspects of the project is the redevelopment of the site near Kent Avenue, where a new building is planned as a model for future development. The overall master plan, developed by WXY, envisions over 5 million square feet of new space. It's interesting to note that this project is driven by a large investment, with the first phase alone seeing a $25 million commitment for the creation of a manufacturing hub encompassing 26,000 square feet. This hub is designed to support over 100 businesses and is expected to be completed by 2025.
The Navy Yard's history as an industrial complex has a lot of repurposed space, and currently, it has a 99% leasing rate, indicating a strong need for affordable manufacturing space within the city. The transformation of Building 77 into a space for tech and industrial businesses demonstrates the potential of the site, with over 3,000 full-time jobs already generated. The new industrial spaces are meant to be diverse, catering to fields like tech, manufacturing, design, and medical. With 500 businesses currently residing there, the Navy Yard is seeking to establish itself as a hub for both manufacturing and innovation.
The location of the Navy Yard, being in a less dense part of the city with large tracts of land, is also driving a concentration of last-mile delivery facilities in the area. One of the concerns that comes with this type of urban renewal is how it could affect the existing neighborhoods in the long run. It's notable that they're aiming for high automation levels in the new facility, potentially up to 60%. If this trend continues, it could create a higher demand for skilled labor as opposed to the kind of jobs traditionally associated with warehouse operations. It's still unclear how this development will impact employment in the long term, especially concerning the current workforce's skill set. There's a need for careful planning to ensure that any potential job displacement is addressed and that the workforce is prepared for the future requirements of these automated facilities.
They're focusing on a vertical storage model instead of typical warehouse layouts. It's intriguing to see how this approach, claiming a potential 30% increase in storage capacity, will address the constraints of urban development. It appears a significant emphasis is placed on streamlining logistics, which might reduce delivery times by 25% using advanced route planning algorithms. It's a fascinating aspect to consider: how a shift towards modular architecture will allow for a more adaptive response to shifting e-commerce demands and potentially make supply chain management more robust. The center also looks to utilize artificial intelligence to manage inventory, potentially lowering overstocking and understocking by roughly 40%. How this level of AI integration plays out in the long run, considering the complexity of urban distribution logistics, will be interesting to observe.
The facility has a temperature-controlled section for perishable goods, using high-quality insulation to prolong shelf life by possibly up to 20%. Their engineering design for pick-and-pack stations considers ergonomics, focusing on workplace safety and productivity. The proximity of the Navy Yard to transportation hubs suggests a focus on sustainability with a reduced carbon footprint while ensuring fast access to markets. They are also utilizing blockchain for data security, potentially increasing the reliability of shipment tracking. They are also developing a dashboard with real-time analytics, looking to improve decision-making processes for improved operational efficiency. These projects are undoubtedly aimed at improving urban logistics, but it's still unclear how effective these strategies will be in practice. Given the complexity of the urban environment, it will be fascinating to observe how these advanced technologies are integrated and the overall impact they will have on both economic and social aspects of the area.
BlackRock's Strategic Pivot 7 Key Industrial Property Investments Reshaping Urban Development in Q4 2024 - Autonomous Vehicle Testing Facility Launch Drives Detroit Industrial Revival
Detroit's industrial landscape is undergoing a transformation, fueled by the recent launch of the Mcity Test Facility. This 32-acre facility, built by the University of Michigan, is a specialized testing ground for autonomous vehicles, offering both physical and virtual environments for research. The facility's existence underscores Detroit's ambition to become a leader in the development of self-driving technology, attracting research teams and partnerships with companies like NVIDIA to push the boundaries of automated vehicle testing.
The push for federal safety standards related to autonomous vehicle testing highlights a crucial challenge: the absence of clear regulations can hinder technological progress. Mcity's role in advocating for such standards indicates the potential for wide-reaching impact on this emerging industry. It's clear that the development of autonomous vehicles is a complex endeavor that needs robust safety guidelines, especially as these vehicles are expected to interact with existing urban environments and potentially alter transportation patterns.
This initiative showcases a revitalized focus on Detroit's industrial sector and its commitment to innovation. However, the success of this initiative will depend on how well it balances technological advancement with social and environmental implications. The long-term consequences of this revitalization, from potential job changes to effects on urban planning, remain open questions for the city to navigate as it continues to embrace a future shaped by autonomous vehicles.
The launch of a new Autonomous Vehicle Testing Facility in Detroit is generating a buzz, potentially reigniting the city's industrial landscape. This facility, encompassing over 60 miles of test tracks designed to mirror real-world driving conditions—urban streets, suburban roads, and highways—is equipped to test a wide range of vehicles, from small passenger cars to large trucks.
It's anticipated that the facility will attract a wave of tech firms and established automakers, providing them with a carefully controlled environment to refine and verify their autonomous vehicle technologies. Whether this influx of investment can truly revitalize Detroit's tech scene, historically anchored in the automotive industry, remains to be seen.
A notable feature is the integration of advanced sensor technology and 5G connectivity, allowing for real-time data streaming. This instant access to data, with minimal delays, is a significant advantage for engineers, who can monitor vehicle performance in real-time and process massive datasets to glean insights.
The facility is also incorporating a dedicated research and development area, encouraging collaborations between universities and industry players. This collaboration, focused on leveraging local academic expertise in areas like robotics and AI, aims to drive innovation.
Safety is naturally a key concern. The facility includes a sophisticated control center with advanced monitoring and communication systems to improve decision-making and safety during testing. While this is a thoughtful approach for a field rife with experimental technologies, it remains to be seen if it can truly mitigate the risks inherent in testing these vehicles.
An intriguing aspect is the facility's design that simulates real-world traffic congestion and unexpected events autonomous vehicles might encounter. This rigorous approach challenges the AI systems in a way that pushes the boundaries of how these machine learning algorithms adapt to unpredictable driving situations.
It's anticipated that the facility's construction will create roughly 2,500 jobs, representing a substantial investment in Detroit's economy. These jobs will encompass a variety of roles, from engineering to facility support, offering much-needed employment opportunities.
The site also includes a public engagement component, with an educational center designed to educate the public about autonomous vehicle advancements. This proactive outreach strategy is crucial for fostering public discourse about the integration of this technology into everyday life, while also promoting transparency.
Conveniently situated near existing automotive supply chains, the facility is likely to minimize logistical expenses for participating companies. This proximity could also potentially speed up the prototyping and iterative development of these technologies, facilitating a faster transition towards commercial adoption.
Further plans to incorporate electric vehicle testing into the facility's capabilities demonstrate its flexibility to adapt to the evolving automotive landscape. This proactive strategy ensures the facility remains relevant as the industry rapidly transitions towards electric propulsion. It will be fascinating to watch how this facility shapes the future of autonomous vehicles and Detroit's industrial landscape in the coming years.
BlackRock's Strategic Pivot 7 Key Industrial Property Investments Reshaping Urban Development in Q4 2024 - Green Industrial Campus Development Reactivates Pittsburgh Steel Site
A former steel mill site in Pittsburgh, Hazelwood Green, is undergoing a transformation into a modern industrial campus with a focus on sustainability. This 178-acre site, once known as Almono, is being redeveloped into a high-tech center with a mix of residential and commercial uses, led by the real estate firm Tishman Speyer. The project emphasizes incorporating green spaces and community features into the design, aiming to create a more vibrant and connected urban environment. The proximity of research powerhouses like Carnegie Mellon and the University of Pittsburgh could fuel innovation and collaboration within the development.
While this revitalization has the potential to inject new life into the area and offer a range of economic benefits, the project will undoubtedly face the inherent challenges of balancing development with community needs. Striking a balance between economic growth, social equity, and environmental considerations will be crucial for ensuring the long-term success and positive impact of this ambitious project. The question of how effectively the redevelopment can integrate the existing community while attracting new residents and businesses will be central to the Hazelwood Green story.
The Hazelwood Green project in Pittsburgh is transforming a 178-acre former steel mill site into a "Green Industrial Campus." This site, once known as Almono and owned by prominent Pittsburgh foundations, was a major steel producer for the nation before its decline. Now, it's being repurposed as a high-tech center with a blend of residential and commercial spaces, led by the global real estate developer, Tishman Speyer. Its proximity to Carnegie Mellon University and the University of Pittsburgh could potentially fuel research collaborations.
The redevelopment is ambitious, potentially creating a facility exceeding 1 million square feet, which would be one of the largest industrial projects in Pittsburgh since the steel industry's downturn. It's aiming to incorporate advanced robotics and automation alongside traditional manufacturing processes, possibly resulting in productivity gains as high as 50%. This could significantly alter the local job market, potentially requiring new skills and creating a shift in the kinds of employment opportunities available.
The planned integration of data analytics and machine learning tools is intriguing, with projections suggesting a 30% reduction in downtime through predictive analytics and optimized production scheduling. This focus on smart technologies is a hallmark of the modern industrial approach, with efficiency and adaptability being primary goals.
A key aspect of the design is its modular construction, which allows the facility to quickly adapt to changes in market demand. This approach is expected to reduce construction waste by 20-25%, showing a commitment to more sustainable practices.
The redevelopment also aims to acknowledge the site's historical importance. The developers plan to retain aspects of the industrial past, potentially creating a hybrid space where modern manufacturing practices are juxtaposed with reminders of the area's heritage. This aspect might make it appealing to research focused on integrating new materials and manufacturing approaches into existing structures.
The project emphasizes workforce development through training programs focused on automation and supply chain management. This initiative may change the local labor market, possibly increasing wages by 15%. It's an attempt to ensure local workers have the skills needed for the new industries moving into the area.
Sustainability is a core aspect, with the inclusion of advanced solar power infrastructure to reduce energy costs by up to 40%. This highlights a shift towards integrating renewable energy into large industrial facilities.
The developers are focusing on high-frequency shipping and receiving, with specialized loading docks designed to handle over 100 trucks per hour. This capacity is designed to meet the increasing demand for rapid fulfillment and delivery in today's urban environments.
Lastly, the project has caught the attention of local governments and educational institutions, fostering collaborations that could transform the campus into an industrial research and innovation hub. These partnerships represent an attempt to create a synergistic relationship between industry, education, and the local economy.
While this project shows a commitment to revitalization, questions still remain about how the redevelopment impacts the surrounding community and the long-term environmental consequences. Nevertheless, it serves as an example of how industrial landscapes in urban environments can be reimagined for the future, embracing technological advancements while acknowledging their historical context.
BlackRock's Strategic Pivot 7 Key Industrial Property Investments Reshaping Urban Development in Q4 2024 - Data Center Complex Investment Modernizes Northern Virginia Tech Corridor
BlackRock's investment focus on data centers is a key factor in how Northern Virginia's technology sector is evolving. The region has seen a massive surge in data center development, with a 24% increase in inventory over the past year, indicating strong investor interest and the region's appeal to companies like Amazon and Google. This growth, spurred by the increasing demand for cloud services, transforms the technological landscape of Northern Virginia. However, concerns arise about managing the growth. Can the area maintain low vacancy rates as this sector continues to expand? Will infrastructure, such as power and water, be able to keep up with the increased demands of these data centers? While this boom undoubtedly has positive economic implications, it also highlights the importance of acknowledging the environmental impacts and resource implications of such rapid technological development in an urban area. This shift towards a data center hub in Northern Virginia offers a compelling illustration of both the potential upsides and the inherent complexities of modern urban industrial growth.
BlackRock's recent investments highlight a significant shift towards industrial properties, particularly data centers, in the Northern Virginia tech corridor. The region has become a hotspot for this industry, and it's easy to see why: it's strategically located, offers relatively affordable energy, and sits close to major internet infrastructure. These elements have propelled Northern Virginia to the forefront of the US data center scene, accounting for a significant share of the national capacity.
The projected growth is astounding. We're talking about an increase of potentially a million square feet per year in data center space. This rapid expansion is being fueled by the surging demand for data processing—think cloud computing and the ever-increasing reliance on data analytics. While this expansion signifies massive growth in data capacity, it's also fascinating to think about the impact on the region's workforce. There will be a need for a workforce trained in data center management and IT infrastructure, as well as professionals skilled in data security. This could reshape the regional labor market in interesting ways, as the demand for specialized skills rises.
A big question surrounds energy consumption. Data centers already consume a significant chunk of energy nationwide, and as AI and machine learning become more ubiquitous, that consumption is likely to increase further. Researchers and engineers are tasked with figuring out how to manage this rising energy demand without straining resources. Interestingly, some of the new data centers are using innovative liquid cooling systems instead of the more conventional air cooling. These new systems can potentially reduce energy usage by a substantial margin—up to 30% in some cases. It's fascinating to see how these new cooling technologies are potentially changing the energy consumption paradigm within the industry.
The drive towards faster data processing is another significant driver of the growth. Reducing latency—the delay in data transmission—is becoming paramount for certain tasks. We're seeing an increase in edge computing solutions in Northern Virginia data centers, capable of significantly reducing latency, potentially as much as 80%. From a network engineering viewpoint, these developments have the potential to greatly enhance the user experience, though the implementation and upkeep of these solutions is far from trivial.
Interestingly, the influx of data center investment is also having an effect on real estate. The demand for land suitable for data center construction is pushing up property values, sometimes converting land originally meant for residential or light industrial use into these high-value facilities. This trend raises concerns about the potential impact on local communities, their character, and access to services and resources.
The design and operation of these new data centers are also fascinating. We're seeing specialized designs, optimized for high-density computing tasks that cater to power usage and efficiently utilize space. With the rapid pace of advancement in server technology, facilities that can manage and optimize power consumption are becoming increasingly important. In addition, with growing concerns about security breaches and the value of the data these centers house, cybersecurity has become a central consideration in their design. This heightened emphasis on security measures, some believe, could even become a way to differentiate one facility from another when attracting clients.
Ultimately, this boom in data center construction is having a significant impact on Northern Virginia. Local governments are facing new challenges—addressing zoning regulations, determining the proper use of tax incentives, and planning for the necessary infrastructure improvements to support the increasing needs of this data-driven economy. The challenge for the area will be to find the balance between this rapid economic growth and its effect on urban development and the potential for urban sprawl. This growth in data centers isn't simply a regional phenomenon, it represents a larger trend that we will be observing for years to come.
More Posts from urbanplanadvisor.com: